Wilson NC Heating & Air Conditioning Services
Expert Local HVAC Services in Wilson, NC
Are you in need of top-quality HVAC services in Wilson, NC? Look no further than Jackson & Sons! In business since 1974, we take pride in serving our community with expert air conditioning and heating repairs, replacements, new installations and maintenance. Our highly trained and knowledgeable HVAC technicians provide same-day service if possible, ensuring that you never have to suffer in discomfort for long. Plus, we offer a range of indoor air quality products, ductwork repair and installation and dryer vent cleaning to keep your home or business comfortable and healthy.
When it comes to residential AC repair, we are the top-rated HVAC company in Eastern North Carolina. But don t just take our word for it – read some of our reviews below to see what our satisfied customers have to say about choosing Jackson & Sons. With us, selecting the right HVAC company is an easy choice that will leave you comfortable all year round! Call (919) 636-6222 now.
Local Reviews
for Wilson, NC
Customers say: The reviews exhibit a positive overall sentiment, with a significant number of reviews expressing satisfaction and praise for the services provided by Jackson and Sons. The positive reviews highlight aspects such as excellent service, polite and informative technicians, quality installations, and friendly and helpful office staff. The recurring themes in the positive reviews include professionalism, punctuality, and the ability to address customer concerns effectively. However, there are also a few negative reviews, which primarily focus on issues such as delayed response times, scheduling conflicts, and dissatisfaction with the quality of work. The negative reviews mention specific instances where customers experienced problems or were not completely satisfied with the services provided. Overall, the sentiment of the reviews is positive, with a slight inclination towards the positive side. The recurring themes in the positive reviews indicate that Jackson and Sons generally provides high-quality services and strives to meet customer expectations. However, it is important to note that the negative reviews should not be overlooked, and the company should continue to work towards improving its services and addressing any issues that may arise.
Our Reviews by City
Great, professional, and friendly.
Donna - Wilson, NC 27893
I always get Great service from Jackson & Sons. Tyler was outstanding
WilsonNC27893 35.6575-77.91



Great Company
Donna - Wilson, NC 27893
I won't use any other company. Great team that does a great job...everytime.
WilsonNC27893 35.6575-77.91



excellent service
Heidi - Wilson, NC 27893
WilsonNC27893 35.6425-77.9125




Great technician!
David - Wilson, NC 27893
Kenny was great, very professional!
WilsonNC27893 35.7375-77.92



Excellent good job
BYNUM - Wilson, NC 27896
WilsonNC27896 35.745-77.955




Always reliable
Donna - Wilson, NC 27893
Always first rate!! Great, dependable service.
WilsonNC27893 35.6575-77.91



Great people and service
WILLIAMS - Wilson, NC 27896
WilsonNC27896 35.77-78.0225




Service review survey
WILLIAMS - Wilson, NC 27893
I always request Matt. Matt always does a great job, answers my question, and very thorough.
WilsonNC27893 35.6425-77.9125



Great service
AL - Wilson, NC 27893
Called for assistance for a demo on my new unit and had a crew come out the same day. Excellent experience
WilsonNC27893 35.7475-77.9925



Excellent Experience
AL - Wilson, NC 27893
Great service and professionalism.
WilsonNC27893 35.7475-77.9925



Overall Great Job
WILLIAMS - Wilson, NC 27893
They took the time to answer my questions and concerns. The work was done in a timely manner. Overall did a good job.
WilsonNC27893 35.6425-77.9125



Great service!
3HC - Wilson, NC 27893
WilsonNC27893 35.7475-77.935




Good Service just wished they had found the problem before the 3rd technician
Karyn - Wilson, NC 27893
I purchased the preferred service package this past summer. Since the technician came out yesterday for the 6 month’s check… my service package had expired in just one day. So no discounts on parts. The technician yesterday supposedly cleaned and checked everything but failed to turn the power source back on. He then checked the temperature before he left stating it was putting out 80 degree air and said it was fine. When I awoke this morning, not even 14 hours after the technician left, the temperature I. Our house was 64 degrees. My only wish would have been a more thorough inspection before today.
WilsonNC27893 35.6525-77.9125



Excellent
RAPER - Wilson, NC 27893
WilsonNC27893 35.6425-77.9125




great service
BROOME - Wilson, NC 27896
Great service, the service technician was very nice and took the time to go over his findings and estimator promptly provided replacement estimates
WilsonNC27896 35.74-77.9575



Excellent job
BYNUM - Wilson, NC 27896
Explain very well
WilsonNC27896 35.745-77.955



Great service!
3HC - Wilson, NC 27893
WilsonNC27893 35.7475-77.935




Great Maintenance Visit!
David - Wilson, NC 27893
Great maintenance visit, feeling more confident and knowledgeable about the units and their readiness!
WilsonNC27893 35.7375-77.92



Fast response
JONES - Wilson, NC 27896
Friendly and knowledgeable
WilsonNC27896 35.79-77.93



Great service!
3HC - Wilson, NC 27893
WilsonNC27893 35.7475-77.935




Great service!
3HC - Wilson, NC 27893
WilsonNC27893 35.7475-77.935




Great service
Charlie - Wilson, NC 27896
No better service
WilsonNC27896 35.77-78.0225



I made the right choice!
Williams - Wilson, NC 27893
I would recommend Jackson & Sons to anyone. They have always provided excellent service for my business and home.
WilsonNC27893 35.695-77.9225



Excellent service
RAPER - Wilson, NC 27893
WilsonNC27893 35.6425-77.9125




Excellent Service
Karyn - Wilson, NC 27893
Very knowledgeable, courteous, fast service for the repair of our air conditioner!!
WilsonNC27893 35.6525-77.9125



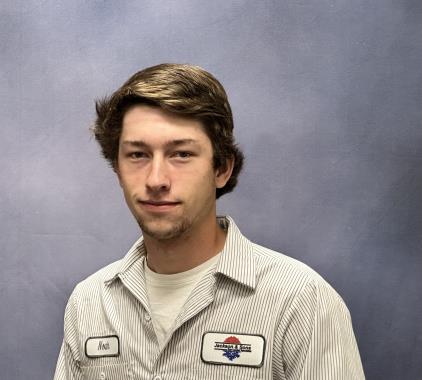
Noah C.
Upon arrival tech found failed thermostat, replaced after approval. System is back up and cooling. Collected service call and billed repair per office.
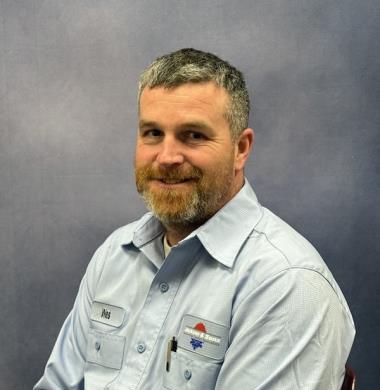
Wes B.
Tech Performed CMA Inspection 5 Split Systems. Systems tested good and working as expected. Fan Capacitor tested weak due for failure provided a estimate — Fan Capacitor Condenser #4 tested weak 4.23/5 mfd
Chris S.
Met with customer to provide price to replace Unit 5.
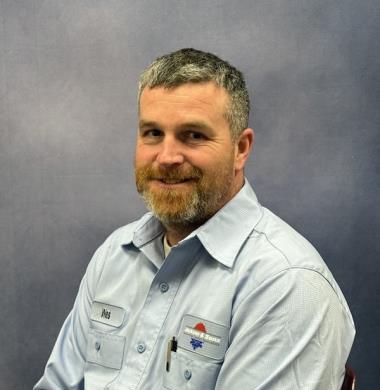
Wes B.
—Tech Performed CMA Full Service 8 Split Systems operating as should. — Blower Capacitor on Air Handler #6 tested weak 9.33/10 mfd. Recommend replacement the capacitor due for failure. Provide a estimate for capacitor. —Condender Fan Motor on System #8 is failed. Provide an estimate for replacement.
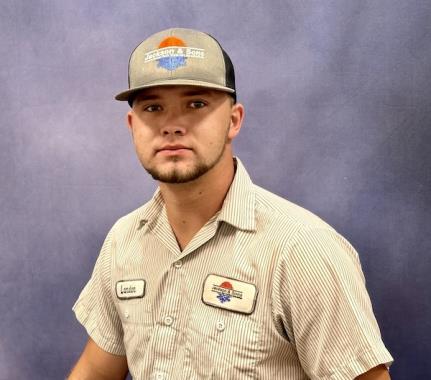
Landen H.
Tech washed and serviced both systems and found no challenges at this time both systems are fairly new customer extended 2 sys Psa 2 times a year via check. Both units are up heating after todays maintenance.
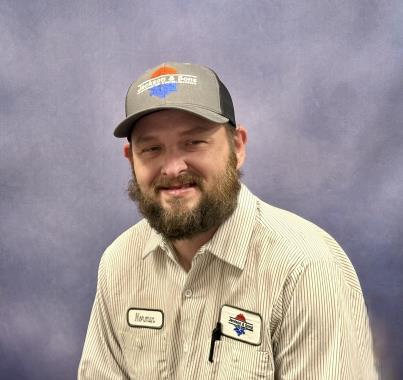
Norman A.
Found leak to be coming from frigerator when you when call for water it start drip from bottom of refrigerator turn water of to refrigerator for can get it look at
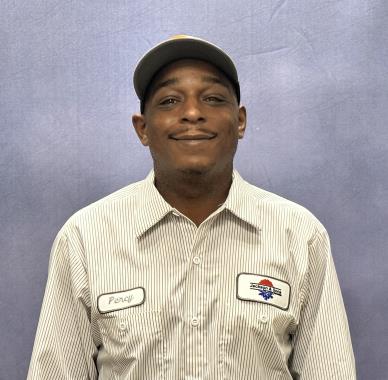
Percy M.
Performed CMA full service on 2 Package Heat Pump systems, 2 Split systems, and 1 Gas Package system. - Package Heat Pump system #1 is operating properly and cooling properly with a Delta T above 18 degrees. - Package Heat Pump #1 fan capacitor rated 20 mf tested weak at 19mf, capacitor is due for failure, recommend replacement of capacitor. - There is an estimate attached to this invoice for replacement of fan capacitor. - Package Heat Pump #2 not in operation at this time, thermostat not functional upon arrival. - Tech consulted with customer about options for Package Heat Pump #2, customer stated system controls a part of the building that is not used and does not want options for getting system back up and running. - Split system #1 in office are is performing and cooling properly with a delta T above 18 degrees system has no challenges at the current time. -Split system #2 which services electrical room is performing properly and has a delta T of above 18 degrees. - Split system #
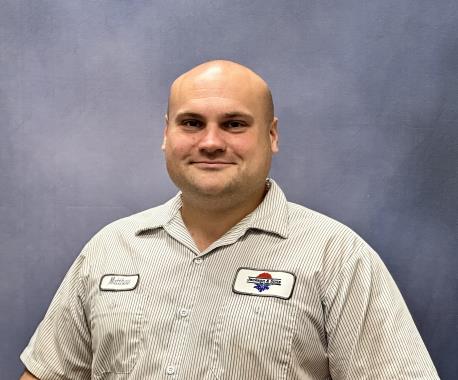
Matthew L.
Tech confirmed E1 and E2 on thermostat 4. Found the error codes online refer to heat failure and cooling failure. RTU4 has a 2 flash lockout error at RTRM board. Blower is running. System is not heating. Duct detector does not appear to be tripped. Tech reset lockout with power cycle and ran through each mode of operation at test pins. Recorded refrigerant pressures and amp draws. System has a two stage compressor and a single stage compressor and heat strips. Four heat stages total. Tech was unable to duplicate lockout. System is back operating in heat. No charge for callback.
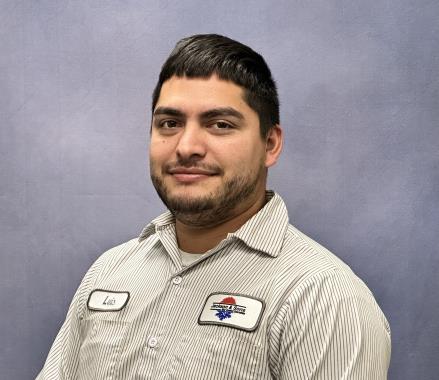
Luis R.
Technician found fuse was blown. System is back side where they are remodeling. S#595L upon replacing fuse te h also found thermostat display was lighting up but blank technician tried to reset multiple times display would still not turn on. Technician quoted out thermostat replacement Danny approved. System is operating properly at this time.
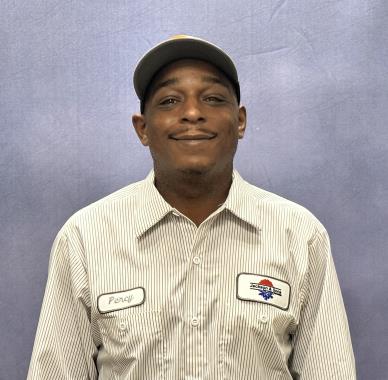
Percy M.
PERFORMED CMA INSPECTION ON 3 ROOFTOP GAS PACKAGE SYSTEMS, 1 MAKE UP AIR SYSTEM AND 2 EXHAUST FANS. ALL SYSTEMS ARE PERFORMING PROPERLY AT THIS TIME. FAN , COMPRESSOR AND BLOWOR MOTOR AMPERAGE CHECKS WERE INSIDE CORRECT SPECIFICATIONS. DELTA T CHECKS WERE OVER 20 DEGREES DIFFERENCE FROM SUPPLY TO RETURN. TECH FLUSHED DRAIN LINES AND ADDED CONDENSATE DRAIN TREATMENT TABLETS TO DRAIN PANS. TECH COMPLETED FILTER CHANGE OF 4-16x20x2, 6-16x24x2, AND 4-18x24x2 FILTERS. THERE ARE PICTURES AND A PERFORMANCE REPORT ATTACHED TO THIS INVOICE.
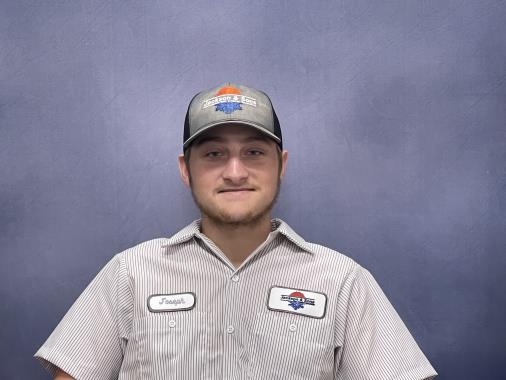
Joseph C.
Upon arrival customer stated city was working on power and when they turned it back on the system never started. Customer already found breaker tripped and reset system is running, customer didn’t want system to be inspected further. System is 40 years old tech recommended replacement due to age customer stated he is interested but is just unable to do at this time and will call back when ready.
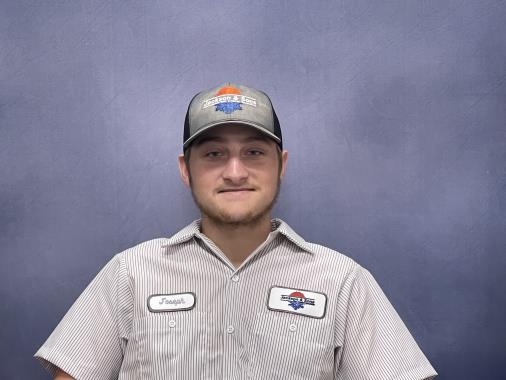
Joseph C.
Tech found E1 and E2 code for coil temp sensor on RTU4, tech inspected and found sensor testing to spec, system is operating properly tech found lots of water in electrical compartment coming in through cracks, tech sealed with silicone and insulation tape. No further challenges at this time.
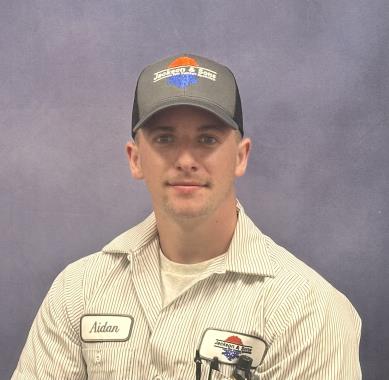
Aidan T.
- Tech found loosely secured door panel on the Trane gas furnace that serves the front offices and lobby area, deactivating the door switch and de-energizing the electrical circuit. - Re-secured panel and taped for reinforcement. Confirmed proper operation with delta T reading 47 degrees. System is heating normally at this time.
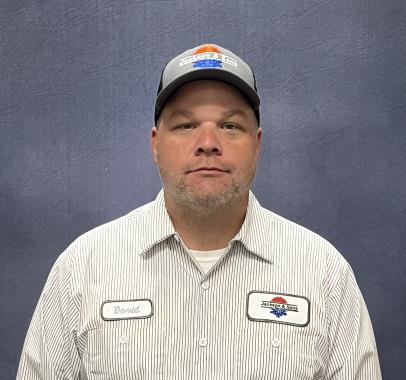
David S.
—Performed CMA Full Service on 5 Rooftop Package Heat Pumps and 2 Mini Split Heat Pumps. —RTU-1 2022 Trane 8.5 Ton Package Heat Pump: Condenser coil slightly frosted upon arrival. System operated defrost in Test Mode without challenges. System operating pressures should be monitored closely at future services. —All systems operating with acceptable temperature differential at this time. Replaced filters, flushed drain pans and traps, tested electrical and temperatures, cleaned and washed units and coils.

Chris A.
Tech washed and serviced unit. Tech found no challenges at this time. Customer extended but changed to a monthly plan. Will call office to discuss card information. Unit is heating with a delta T of 22.

Amber W.
Install New 3 Ton Duct System With Return Includes Plasma Air
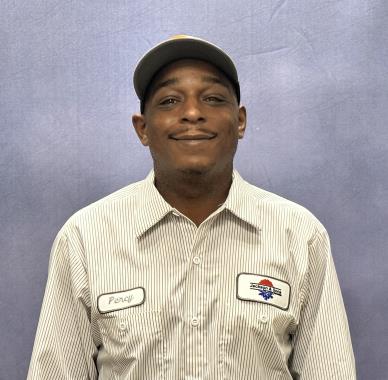
Percy M.
PERFORMED CMA FULL SERVICE ON 1 SPLIT SYSTEM AND 1 PACKAGE HEAT PUMP SYSTEM. SPLIT SYSTEM AND PACKAGE HEAT PUMP SYSTEM ARE BOTH OPERATING PROPERLY AT THIS TIME. TECH CHANGED FILTERS AND FLUSHED DRAIN LINES ON BOTH SYSTEMS. TECH CHECKED FAN,COMPRESSOR AND BLOWOR MOTOR AMPERAGE FOR. BOTH SYSTEMS, AMPERAGE CHECKS WERE INSIDE CORRECT SPECIFICATIONS. THERE ARE NO ISSUES WITH EITHER SYSTEM AT THIS TIME. THERE ARE PICTURES AND A PERFORMANCE REPORT ATTACHED TO THIS INVOICE.
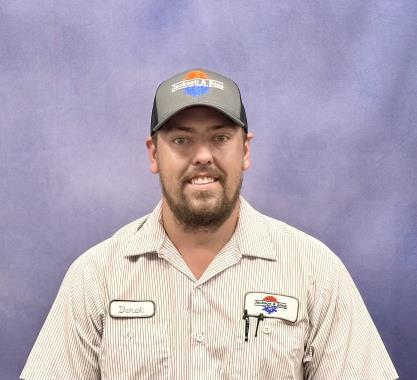
Derek J.
Upon arrival tech was informed system was making a noise and electric bill has been extremely high. Tech found system ramping up as need when calling for heat and aux heat and that’s where noise was coming from. Tech did find condenser not running even though it was calling. Further inspected and found no line voltage due to a tripped breaker in main panel. Megohm compressor and it read bad indicating internal windings had insulation deteriorated. Checked compressor to ground and had a resistance reading as well, compressor has failed. System is still under warranty. Tech emailed estimate to replace compressor. Tech also emailed estimate to replace outdoor temp sensor which has also failed. Customer is going to reach out to contractor that installed system to see if they will cover and if not will contact office to make repairs.
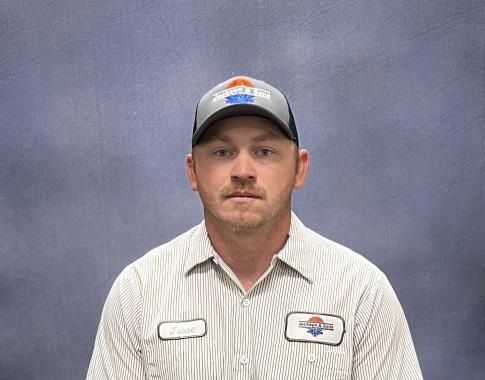
Jesse J.
Install (2) Trane 2.5 Ton Split Heat Pump Systems, An 18K Mini Split, & (2) 12K Mini Split Gas Heaters Will Be Removed & Gas Lines Capped
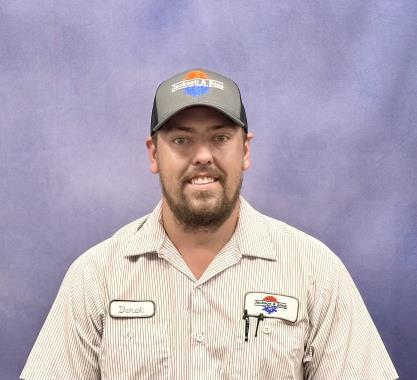
Derek J.
Upon arrival tech was informed system for office was not cooling. Inspected and found condensing unit not running or receiving 24v on the Y circuit. Inspected air handler and found ezt226 safety switch tripped. Removed top and plunger on bottom was broken off and wedged underneath. Tech replaced with new and condenser came on. Poured water through drain line to ensure no blockage. System is back operational at this time.
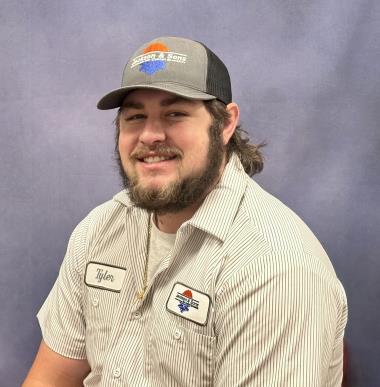
Tyler T.
Tech washed and serviced unit per service agreement, upon inspection tech found duel run capacitor testing below spec, tech recommended replacement of capacitor, customer approved at today’s visit, the system is back up and running and holding a delta t of 20+ degrees

Caleb S.
Emailed customer quote to install new duct system
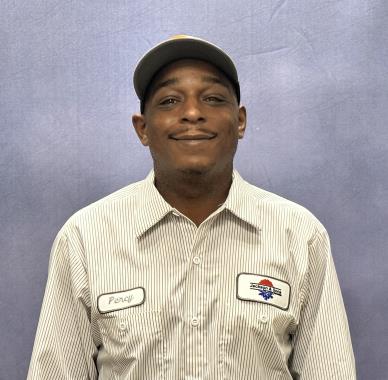
Percy M.
PERFORMED CMA INSPECTION ON 3 SPLIT SYSTEMS. SPLIT SYSTEM #1 BLOWOR MOTOR CAPACITOR RATED FOR 10mf TESTED WEAK AT 6.48mf. CAPACITOR IS DUE FOR FAILURE, RECOMMEND REPLACEMENT OF CAPACITOR. THERE IS AN ESTIMATE PROVIDED FOR REPLACEMENT OF CAPACITOR. SPLIT SYSTEMS 1,2,AND 3 ALL HAVE A POWER SWICH IN FRONT OF EVAPORATOR COIL ACCESS DOORS THAT WILL NOT ALLOW ACCESS TO COILS. SPLIT SYSTEM #2 HAS A METAL PIPE THAT HOLDS UNIT UP IN CEILING IN FRONT OF ACCESS DOOR FOR BLOWOR SECTION , CAN NOT ACCESS BLOWOR SECTION ON SPLIT SYSTEM #2. TECH COMPLETED FILTER CHANGE OF 6-20x20x1 FILTERS. ALL SYSTEMS ARE PERFORMING PROPERLY AT THIS TIME. THERE ARE PICTURES AND A PERFORMANCE REPORT ATTACHED TO THIS INVOICE.
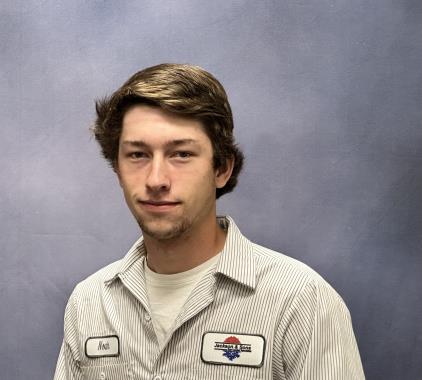
Noah C.
Found error code E1 and 2 at RTU 4 sensor indicating issue with coil temp sensor. Reset system and monitored operation. Tested coil sensor and found no challenges, let system run with no further challenges.

Bryce C.
Duplicate call