Rose Hill NC Heating Air & Conditioning Services
Jackson and Sons has been serving the heating and air conditioning needs of Rose Hill, NC residents and businesses since 1974.
Our reviews below from your neighbors in Rose Hill, NC tell the story of our quality, dedication and commitment to customer service.
Local Reviews
for Rose Hill, NC
Customers say: The reviews exhibit a positive overall sentiment, with a significant number of reviews expressing satisfaction and praise for the services provided by Jackson and Sons. The positive reviews highlight aspects such as excellent service, polite and informative technicians, quality installations, and friendly and helpful office staff. The recurring themes in the positive reviews include professionalism, punctuality, and the ability to address customer concerns effectively. However, there are also a few negative reviews, which primarily focus on issues such as delayed response times, scheduling conflicts, and dissatisfaction with the quality of work. The negative reviews mention specific instances where customers experienced problems or were not completely satisfied with the services provided. Overall, the sentiment of the reviews is positive, with a slight inclination towards the positive side. The recurring themes in the positive reviews indicate that Jackson and Sons generally provides high-quality services and strives to meet customer expectations. However, it is important to note that the negative reviews should not be overlooked, and the company should continue to work towards improving its services and addressing any issues that may arise.
Our Reviews by City
Alex was marvelous
Mike - Rose Hill, NC 28458
Alex was marvelous...on time and work completed quickly...
Good service
Mary - Rose Hill, NC 28458
David C.
Install Trane 3 Ton Package Heat Pump With WiFi Programmable Thermostat
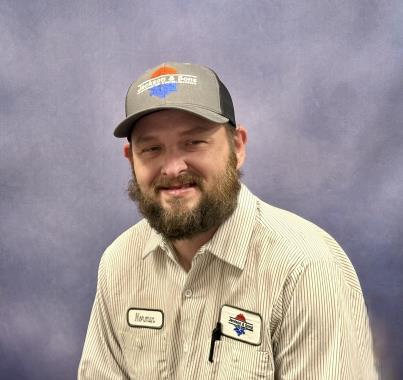
Norman A.
Advise home owner we will remove sheet rock but not replace it. Ran water threw drain for 5 min no leaks water line are great Believe issues to be

Caleb S.
Customer invested in a 3 ton PHP for a mobile home. Consultation Code: ENGN8CMM7
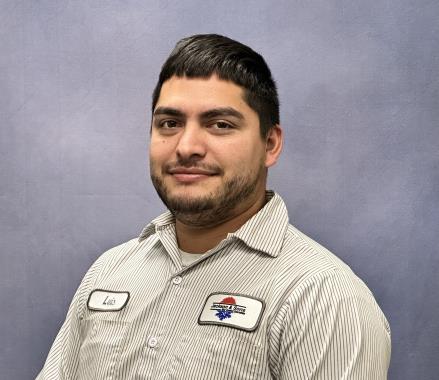
Luis R.
Tech found power to contactor and contactor was being pulled in but not sending the power out. Tech informed customer on contactor findings and informed customer tech will need to replace part in order to further diagnose. Customer approved customer also mentioned allergies. Tech educated customer on plasma Pure air she approved installing. Tech was also informed of plumbing issues and schedule a plumbing call. Upon replacement of contactor tech found condenser engaged and running them kicking off in high pressure within 5 mins system would reach 600psi. Tech cycled cooling mode and found system having higher then normal pressures but running in cooling, ans soon ans tech engage heating mode system shoot up in pressure again indicating fixed orfice was clogged in heating mode. Tech called office to get field supervisor out to give best solution.
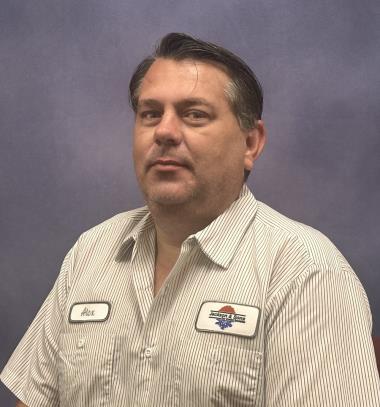
Alex R.
Found defective parts leaking from our previous repair. Replaced the leaking parts with new parts. No other leaks found after repairs this time.
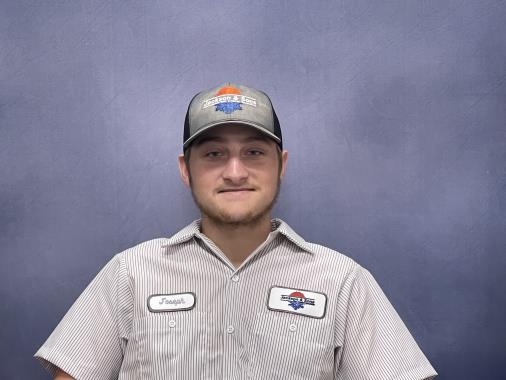
Joseph C.
Tech arrived and found system not running, customer worked on system stated he put new capacitor for fan on. Tech found disconnect was flipped the wrong way tech corrected and system is now running and cooling properly. Fan amps were high tech recommend replacing motor customer is going to take care of it himself.
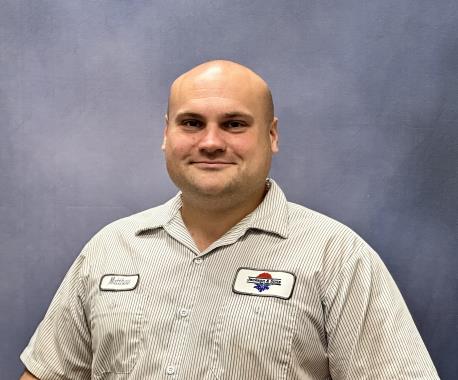
Matthew L.
Pulled tank and replaced tank to boul seal and bolts.
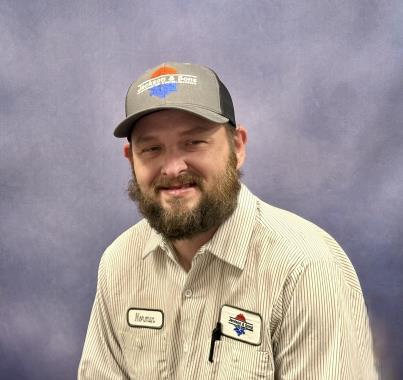
Norman A.
Found clog in 1 1/2 galvanized pipe advice home own It willl need be replaced
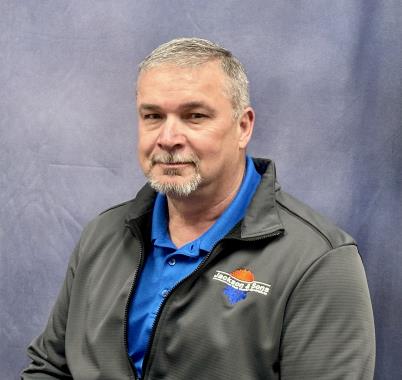
Chris M.
Checked hose bib for leak under house. It is not leaking and I recommended they have the window checked for leaks….window has gaps around the top.
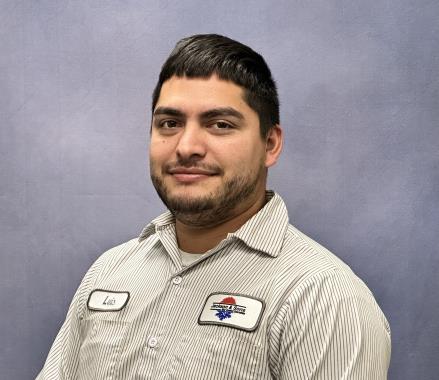
Luis R.
Tech found dual run 70/5 capacitor had failed on compressor side fan side is 4.7 slightly weak. Tech called Justin and informed him on findings he approved replacement with turbo capacitor. Once replaced system started up no issues tech did inform Justin if he had maintenance plan he did not he wants quote on maintenance plan as well. They have 2 straight ac splits and 2 gas furnace
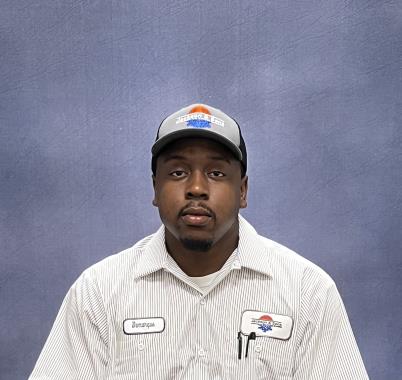
Demarcus M.
UNIT #7, KITCHEN- 4 TON TRANE SPLIT HEAT PUMP
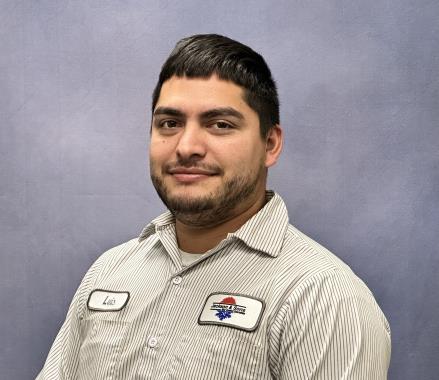
Luis R.
Tech found system pressure were at 52/198 for r22. Tech performed leak search got hits on bottom side of evaporator coil. Compressor ohmed good at this time. Due to age and type od Freon te h recommend replacing system. S#yg2v
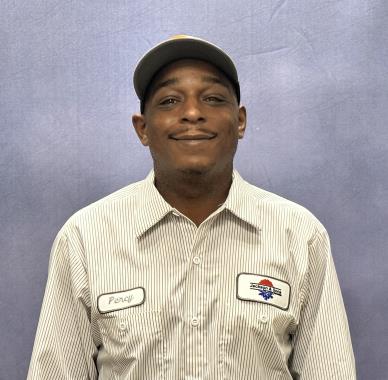
Percy M.
PERFORMED CMA FULL SERVICE ON 10 SPLIT SYSTEMS. SPLIT SYSTEM #1 AIR HANDLERS EVAPORATOR COIL WAS FROZEN ON ARRIVAL, PUT SYSTEMS BLOWER ON TO THAW OUT COIL . TECH CHECKED DELTA T WHICH IS TEMPERATURE DIFFERENCE BETWEEN RETURN AND SUPPLY AND IT WAS 10 DEGREES. DELTA T IS LOW WOULD RECOMMEND FOR IT TO BE AT LEAST 17 DEGREES DIFFERENCE. WILL HAVE TO ADD MORE REFRIGERANT IN UNIT TO SEE IF THAT WAS THE ISSUE. SPLIT SYSTEM #2 COMPRESSOR CAPACITOR RATED FOR 70mf TESTED WEAK AT 66.2mf. CAPACITOR DUE FOR FAILURE. RECOMMEND REPLACEMENT OF CAPACITOR. SPLIT SYSTEM #4 CONDENSER UNITS DUAL RUN CAPACITOR RATED FOR 45/5mf TESTED AT 38.9/5.01mf. TESTED WEAK ON 45{COMPRESSOR SIDE). CAPACITOR DUE FOR FAILURE. RECOMMEND REPLACEMENT OF CAPACITOR. REPLACEMENT OF DUAL RUN CAPACITOR FOR SPLIT SYSTEM #4 SPLIT SYSTEM #7 WAS TURNED OFF UPON ARRIVAL, MULTIPLE I

Bryce C.
Customer just had shoulder surgery and was baby sitting grand daughter. Just wanted pricing emailed to her.
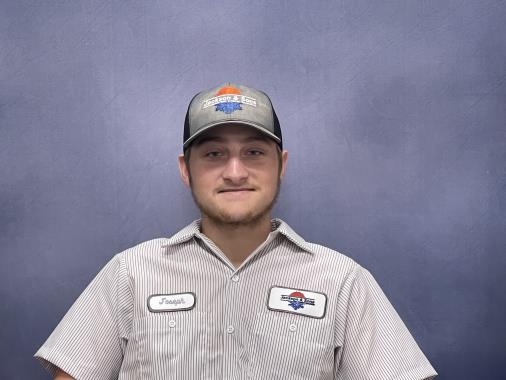
Joseph C.
Tech performed ESA on 1 system. Gas Pack- tech serviced and cleaned system found indoor evaporator coil leaking refrigerant, compressor ohming bad and duct work under sized and in poor condition. Field supervisor out to verify challenges.
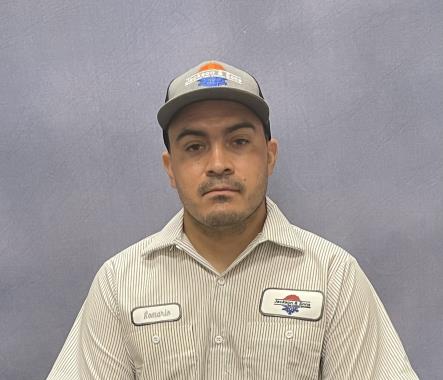
Romario T.
System 4 - Compressor Replacement. Tech pulled vacuum on system and charged with 5lbs and 7oz of R410A, factory charge is 8lbs. Rewired compressor wires and reconnected all other wiring. Will need to return to further diagnose low voltage short due to it blowing low volt fuse as soon as power was turned on. OD Disconnect had 2- 15amp blown fuses, replaced with 2- 30amp for the time being but will need 2- 15 fuses(small ones). Tech finished up charging the system with 3lbs of 410a refrigerant. and corrected the low voltage challenge. Short at the Reversing valve wire was identified. System #4 is back cooling. 30amp fuses at the outdoor unit will be needed to be replaced with 15amp fuses(small fuses).