Nashville NC Heating & Air Conditioning Services
Expert Local HVAC Services in Nashville, NC
At Jackson & Sons, we know how much our customers in Nashville, NC, rely on their heating and cooling systems to keep their homes comfortable. Our local HVAC company offers a full range of HVAC services, from air conditioning repair to ductwork installation, to ensure that our customers' needs are met. Our highly trained and knowledgeable technicians are dedicated to providing top-notch work, offering same-day service whenever possible.
In the industry since 1974, we take pride in our commitment to our community and providing quality workmanship. Our team understands the importance of trust and reliability. Choosing Jackson & Sons for your AC repair, maintenance and other HVAC needs is an easy choice. But don't take our word for it, read our reviews below in Nashville to see why we're the top-rated HVAC company in Eastern North Carolina. We value our customers and are dedicated to providing excellent service every time. So, if you need air conditioning repair or any other HVAC services, give us a call today at (919) 636-6222 !
Local Reviews
for Nashville, NC
Customers say: The reviews exhibit a positive overall sentiment, with a significant number of reviews expressing satisfaction and praise for the services provided by Jackson and Sons. The positive reviews highlight aspects such as excellent service, polite and informative technicians, quality installations, and friendly and helpful office staff. The recurring themes in the positive reviews include professionalism, punctuality, and the ability to address customer concerns effectively. However, there are also a few negative reviews, which primarily focus on issues such as delayed response times, scheduling conflicts, and dissatisfaction with the quality of work. The negative reviews mention specific instances where customers experienced problems or were not completely satisfied with the services provided. Overall, the sentiment of the reviews is positive, with a slight inclination towards the positive side. The recurring themes in the positive reviews indicate that Jackson and Sons generally provides high-quality services and strives to meet customer expectations. However, it is important to note that the negative reviews should not be overlooked, and the company should continue to work towards improving its services and addressing any issues that may arise.
Our Reviews by City
Stellar Customer Service
Emily - Nashville, NC 27856
Professional and thorough! Would recommend to neighbors and friends.
NashvilleNC27856 35.9775-77.9525



Great service as always
CLARK - Nashville, NC 27856
NashvilleNC27856 35.9725-77.9675




Very pleased
CLARK - Nashville, NC 27856
Very professional and knowledgeable
NashvilleNC27856 35.9725-77.9675



Excellent Service
VIRGINIA - Nashville, NC 27856
Bryce was very nice and respectful. He tried to help anyway he could.
NashvilleNC27856 35.9325-77.945



Excellent Service.
VIRGINIA - Nashville, NC 27856
Noah was very nice and respectful. Helped me slot with him being able to come today
NashvilleNC27856 35.9325-77.945



Misdiagnosed
James - Nashville, NC 27856
Wow left a great review about a month ago only to be wronged. Was told I had a leak and needed a new compressor. Both statements were false, BUT Atleast y’all found the initial problem. Not sure if I’ll use this company again.
NashvilleNC27856 35.955-77.9375



Honest, hardworking and reliable
James - Nashville, NC 27856
Donald has been to my house twice. Both times he’s provided excellent service. He explain everything and makes sure we’re good to go before he departs. Very honest as well!
NashvilleNC27856 35.955-77.9375



Excellent service
CLARK - Nashville, NC 27856
NashvilleNC27856 35.9725-77.9675




Great service as always
Dewey - Nashville, NC 27856
NashvilleNC27856 35.9725-77.97




Great service as always
Dewey - Nashville, NC 27856
NashvilleNC27856 35.9725-77.97




Great service
Kathy - Nashville, NC
Exceptional!
NashvilleNC 35.99-77.98



Peace of Mind
Katie - Nashville, NC 27856
We are so glad we found Jackson & Sons. We’ve had a great experience all around from customer service center to the techs who do repairs and maintenance.
NashvilleNC27856 35.995-77.96
Response from Jackson & Sons:
We're glad to hear that you had such a positive experience with us. Thanks for taking the time to leave a review.




Great Service
Dewey Clark - Nashville, NC 27856
Great service
NashvilleNC27856 35.9725-77.9675



Great Service
DEWEY - Nashville, NC 27856
Jason King was wonderful. Wish I could rate him a 6. Very knowledgeable. Went the extra mile to make everything right
NashvilleNC27856 35.9725-77.9675



Great Service!
Heather - Nashville, NC 27856
The technician was very professional and spent the time to explain everything that was occurring. We truly appreciate the time and effort that Jackson and Sons and Eric has put into the issues we have been having with your AC unit.
NashvilleNC27856 35.9525-77.9525



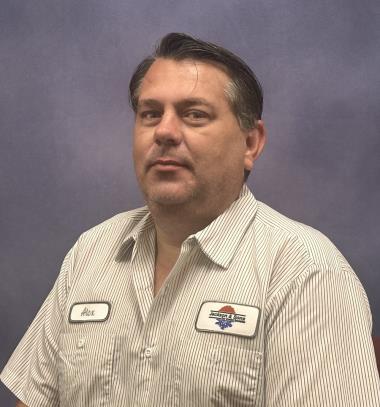
Alex R.
Removed old toilet from guest bath and installed a new American standard toilet. Cleared kitchen sink, drain line and tested with water for approximately five minutes.
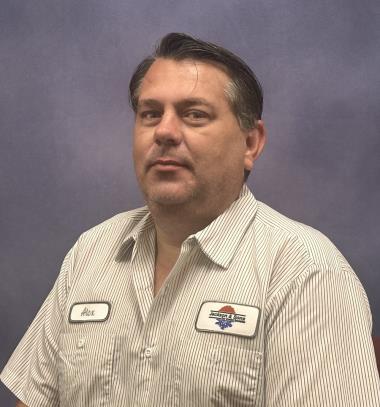
Alex R.
Gave customer an estimate for replacing the guest bath, toilet and running the sewer machine through the kitchen sink, drain line and clearing the drain.

Chris A.
Tech washed and serviced unit, customer not home dad gave access to home. found blower capacitor testing just below tolerance, (6.5/7.5) tech recommended replacing. Customer will think about it (left estimate). Unit is operating properly holding a delta T of 22.

Amber W.
Goodman Packaged Unit GPHH32441A Goodman, GPHH3, 2 Ton, Packaged Unit Quantity: 1 Other Air Quality CUSTOM-29BJHR Plasma Air 602 Quantity: 1 Other Services CUSTOM-0M1HWW ESA Quantity: 1 Other HVAC Add-Ons CUSTOM-BWQ0I5 Goodman HKR10 Quantity: 1 14" Start Collar Quantity: 1 38x27.75 Hood (Goodman "H Model") 2T & 2.5T Package Unit Quantity: 1 38x70 Pad Quantity: 1 Change Breaker JS Quantity: 1 ICM Surge Protector Quantity: 1 Level Pad Quantity: 1

Bryce C.
Provided system replacement. Invested in new system
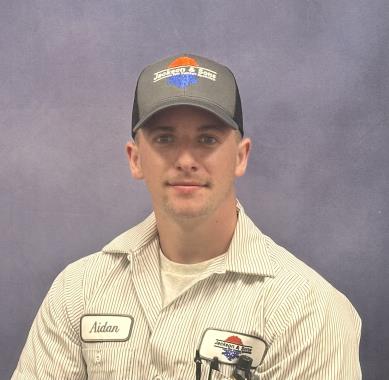
Aidan T.
(Kitchen Packaged Heat Pump) - Tech found failed variable speed blower motor upon arrival. Noted valve cores are leaking and standing refrigerant pressure reading low. Provided estimates for repairs and recommended system replacement on account of expired warranty and costly repairs. - Customer opted to replace the system and requested replacement quote. Turned over to field supervisor. Please channel all communication regarding the replacement of the system through Mr. Wayman: 407-595-2908. Customer is interested in investing in a premium service agreement for the new system. Door will be unlocked for field supervisor. Please make sure backyard gate stays closed.
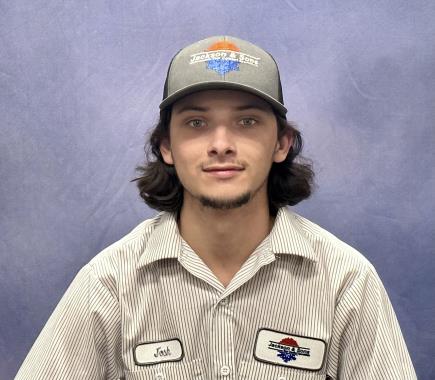
Josh W.
Tech performed esa on one system, tech found no issues at todays visit. System is back on and operating properly after completion of service. All is good at this time.
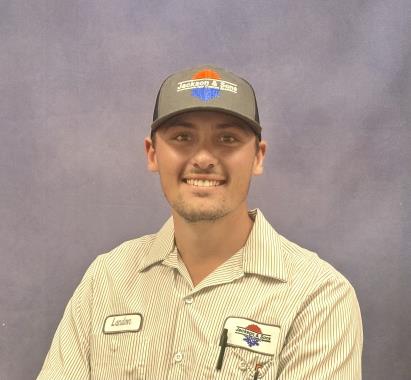
Landon C.
Tech preformed preventative maintenance and serviced system. Tech found UV Bulb to be worn and recommended replacing. Customer did not invest in new bulb at this time. Customer did invest in ESA renewal and system is up and running with a delta t of 20.
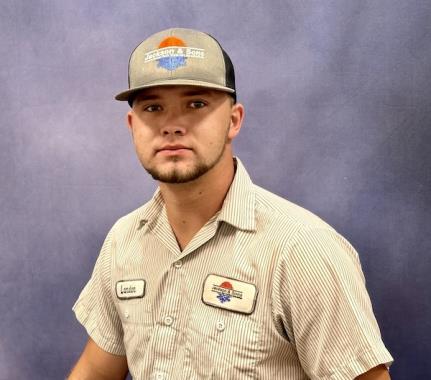
Landen H.
Tech washed and serviced 2 mini splits and 2 package heat pumps tech found no challenges at this time both mini splits where up and cooling with proper delta t. Tech could no check delta t of main home due to dogs and customer having to leave. Customer paid for 2 sys tune up for the mini splits but was not interested in investing or extending at this time will have to call back at a later time.
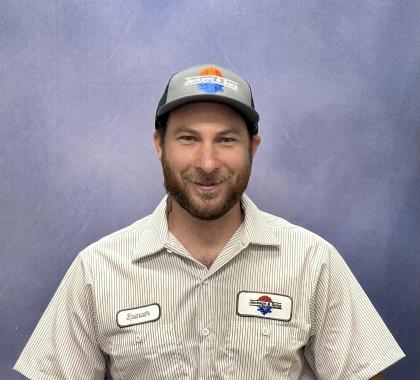
Spencer C.
Tech found secondary pan full of water and float switch breaking power to y. Tech recommended maintenance plan and customer agreed. Tech removed water, cleared drain and tested system. Tech found system is operating properly with normal refrigerant pressures. Tech informed customer evaporator coil is rusty and that caused the clog.
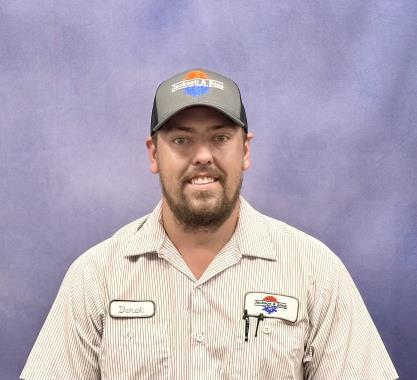
Derek J.
Upon arrival tech was informed system was not cooling. Inspected system and found dual run capacitor had failed. Replaced with new 35/5 capacitor. Tech did not have access inside home due to tenant not being there. Tech jumped 24v to blower and compressor contactor and system came on. Tech informed homeowner that without access inside home to thermostat we could not guaranteed there are no further challenges with the system.
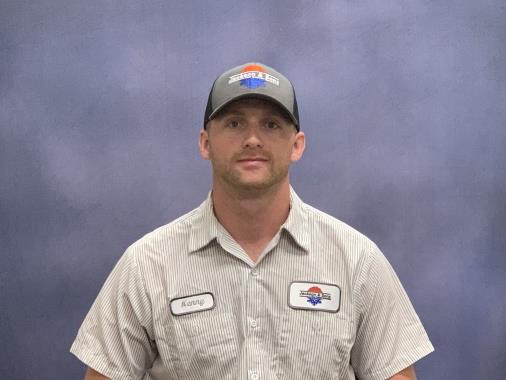
Kenny C.
Upon arrival tech found ceiling had water spots around 2 vents. Homeowner stated they turned the system off once they found ceiling damage. Issue occurred last night around 10pm, tech then ran system for approximately 45mins to an hour to find where water was coming from. Tech inspected duct work, no air leaks or ducts sweating. Also observed refrigerant pressures, made sure drain line was draining properly. Vents are not condensating either, also inspected collars on branch lines, everything is is secured. Could not duplicate issue at todays visit, informed homeowner if issue occurs again to let system run and give us a call.
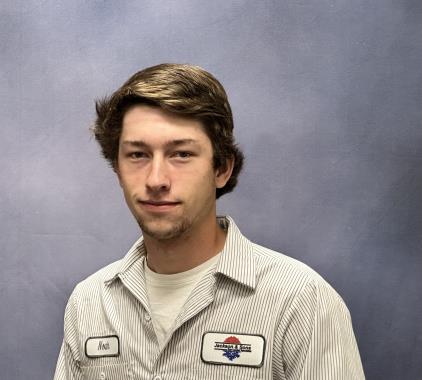
Noah C.
Upon arrival customer stated system has since came back on and began cooling. Found indoor temp displayed at 71 with a set point of 70. Tech monitored system operation and found everything to be operational. Found system running a high head pressure. Tech rinsed coils and had no effect on pressure. Inspected duct system, tested TXV. Tech found no challenges or any indications causing the high head pressure. System may have went out on high pressure switch. Tech stated to call if issue occurs again, system is cooling with an 18 degree delta t.
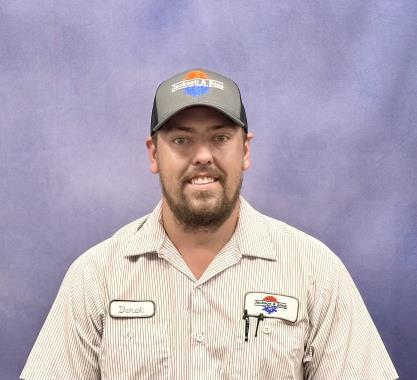
Derek J.
Upon arrival tech was informed evaporator coil was freezing. Tech inspected system and found it low on Freon. Performed leak search and found it leaking at evaporator coil. Homeowner approved charging system with R22 Freon to get system back cooling until field supervisor can come out and get new system quoted. Tech charged with 3lbs of R22 Freon. System is back operational at this time but will continue to leak until a repair or replacement of system is done.
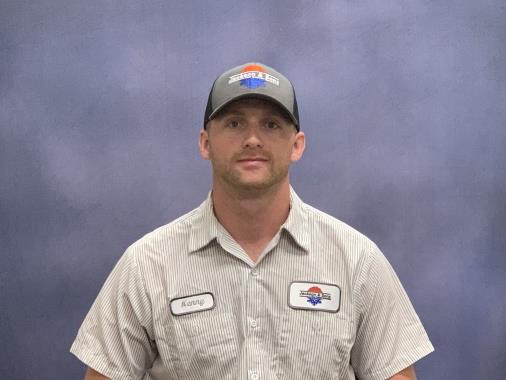
Kenny C.
Upon arrival homeowner stated upstairs system not cooling, tech found failed capacitor, tech replaced capacitor and found high head pressure. Tech noticed filter was extremely clogged. Tech replaced filter and capacitor. System is back up and cooling at this time. Recommended ESA, homeowner stated they are selling home in the near future. System is back up and cooling.
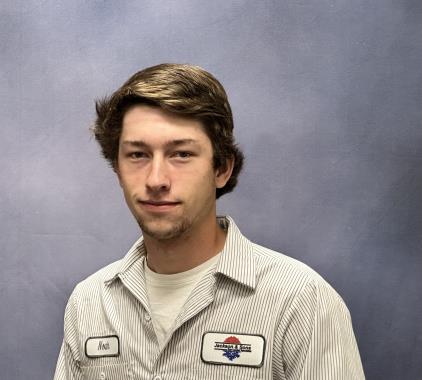
Noah C.
Upon arrival tech found blower running at gas pack but receiving no Y call. Tech removed thermostat and jumped Y circuit and still received no call at unit. Only 4 wires on old side of splice, used white wire in place of Y wire for testing purposes. System came on properly and cooled with white wire confirming a break within Y circuit. Sent estimate on thermostat wire replacement as well as thermostat due to its age. Customer will make a decision for approval. Also need to get quote on CMA.
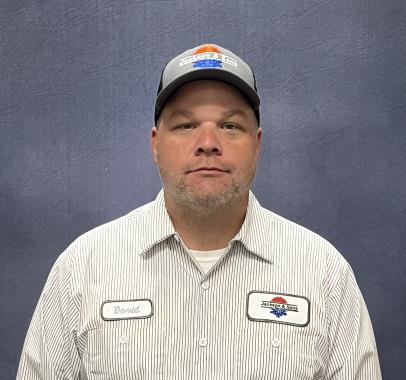
David S.
-Performed CMA Full Service on 8 Split System Heat Pumps. -System 1: No wire for overflow switch on EZ Trap as previously reported. Secondary drain line has float switch. -System 2: No wire for overflow switch on EZ Trap as previously reported. Auxiliary pan has float switch. -System 3: Overflow switch on primary drain line not wired, as previously reported. Wire near unit unused. Recommend minor wiring repair to correct. Air flow restrictions due to return location have been noted prior. -System 4: No wire for overflow switch on EZ Trap as previously reported. Secondary drain line has float switch. Condensate pump not running when full. Cleared drain line with compressed nitrogen. Drained collection pan and added water back. Pump still not running and alarm light shows. Recommend replacing pump or running drain line to nearby floor drain. Unplugged pump due to excessive heat on pump motor. Air handler will drain onto floor to floor drain for time being.
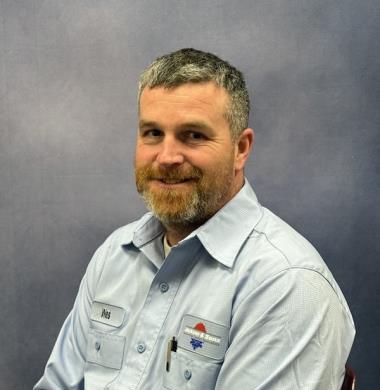
Wes B.
Tech returned to investigate all 3 systems not working Kitchen - tech found the system to be operational. Upon arrival the thermostat was satisfied, tech bumped set temperature down and system began cooling properly. Dining room 866D - tech found this system to be operating as well. Tech bumped set temp down and found the system to be cooling, supply temperature was 59 degrees. This one is having to work and keep up for the other dining room system. Dining Room 907D - upon arriving, technician did not find the system operational. Power was turned off and then restored. Blower came on as normal, and then compressor and outdoor fan. System ran for a few minutes and then cut off. This system has a history of refrigerant related challenges, and this appears to be a continuation of this. Prior to leaving tech confirmed all thermostats satisfied at set point.
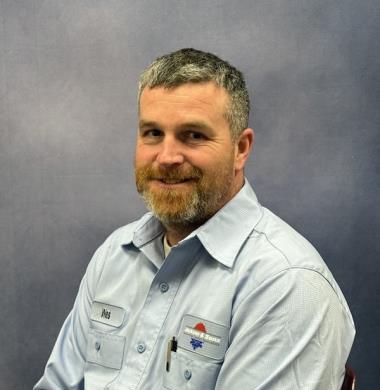
Wes B.
Performed CMA inspection on 3 Gas Package Units (coils washed on kitchen unit), 2 make up air systems, and 4 exhaust fans. Gas Pack (Kitchen) - technician found the system to be operating within spec at today’s visit. All electrical tested good. Delta t observed was 18 degrees. Filters changed. Gas Pack (Dining - 866D) technician did not find any major challenges while servicing equipment today. The system is cooling properly, delta t observed was 20 degrees. Blower belt tightened - upon arrival the blower was making a loud squeaking noise. Upon inspection, tech found the belt to be loose. Once tightened, the noise subsided, system working correctly. Filters changed Gas Pack (Dining - 907D) upon arriving to the system the tech did not initially find any challenges. System was cooling good. Upon further inspection technician found Y2 thermostat wire disconnected. This is likely due to previous service. Notes from 4/6/23 state, circuit 2 to be an estimate 13 pounds low on refrigerant
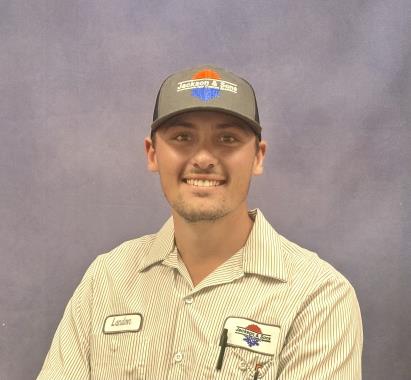
Landon C.
Tech performed maintenance per service agreement. Tech found 40 MFD capacitor testing week 35.8 MFD. tech also found bacteria buildup accumulating inside blower fan. Tech cleaned bacterial buildup and consulted homeowner about capacitor. Tech replaced 40 MFD capacitor at $192.82 via MasterCard after homeowners approval. Homeowner has a UV bulb that is still glowing. Tech explained that it’s not as effective anymore. Homeowner stated he may replace on next visit. tech left one 20 x 20 filter with homeowner. System is operating properly at this time.
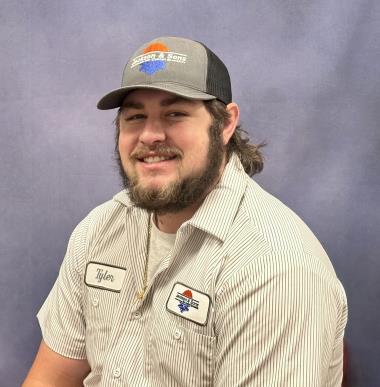
Tyler T.
Tech performed ESA on 1 system. Tech found no challenges or concerns with system/operations. Tech thoroughly cleaned inside and outside of system. System is operating properly upon departure. Homeowner extended ESA plan via card.

Bryce C.
Customer planning to invest in new system will know for sure this evening
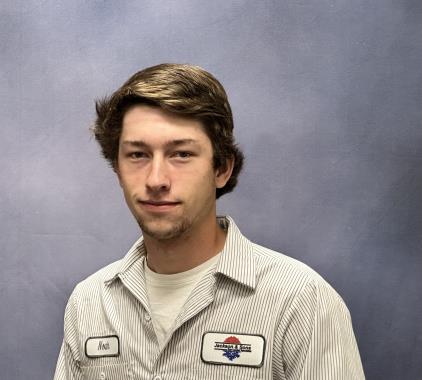
Noah C.
Tech arrived to verify findings of previous company’s diagnosis. Tech confirmed diagnosis was in fact correct. Tech found a failed compressor, cracked heat exchanger, leaking evaporator coil as well as a failed variable speed motor/module and control board. System is 12 years old. Price of repair will outweigh price of replacement. Tech gave details to home warranty company per request, need to have a supervisor come out tomorrow after 12 to give replacement quote. Tech left power to system off. Collected house call fee by card.
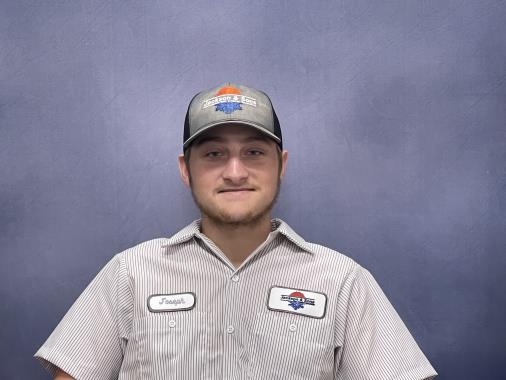
Joseph C.
Tech found leaking evaporator coil lots of rust and corrosion and outdoor fan motor over amping. Tech also found that heat strip pull out diss connect is bypassed home owner is unsure why, tech inspected pull out is missing tech suspects this is why someone bypassed. Field supervisor out to verify tech didn’t clean system per customer request.
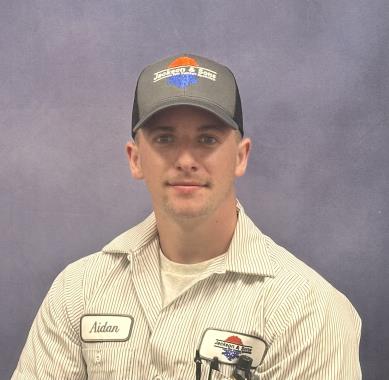
Aidan T.
Tech performed two system ESA, tech made recommendations for each unit. Bryant package-tech found bacterial build up in unit and recommended plasma, tech also recommended surge protection to protect major components from power surge and potential lightning strike. Payne package- tech recommended surge protection to protect major components from power surge and potential lightning strike.tech found no issues with system operation at this time. Both systems are back on and operating properly at this time. Customers are interested in adding mini splits to ESA, and said they would add them at next visit due it being TTE at that time. Customers have washable filters.