Mount Olive NC Heating & Air Conditioning Services
Expert Local HVAC Services in Mount Olive, NC
At Jackson & Sons, we understand how frustrating it can be when your air conditioning or heating system isn't functioning properly. Our local HVAC company offers a wide range of HVAC services in Mount Olive, NC, including AC repair and furnace repair to keep you comfortable year-round. Our highly trained and knowledgeable HVAC technicians are equipped to handle any heating or cooling service you may need, from replacements and new installations to maintenance and ductwork repair and installation. We also care about the quality of the air you breathe in your home, which is why we offer indoor air quality products and dryer vent cleaning.
In business since 1974, we take pride in being the top-rated HVAC company in Eastern North Carolina. Our commitment to our community means that we strive to provide outstanding customer service and same-day service whenever possible. We invite you to read our reviews from other satisfied customers in your area and discover why choosing Jackson & Sons for your HVAC needs is an easy choice. Call us today at (919) 636-6222 !
Local Reviews
for Mount Olive, NC
Customers say: The reviews exhibit a positive overall sentiment, with a significant number of reviews expressing satisfaction and praise for the services provided by Jackson and Sons. The positive reviews highlight aspects such as excellent service, polite and informative technicians, quality installations, and friendly and helpful office staff. The recurring themes in the positive reviews include professionalism, punctuality, and the ability to address customer concerns effectively. However, there are also a few negative reviews, which primarily focus on issues such as delayed response times, scheduling conflicts, and dissatisfaction with the quality of work. The negative reviews mention specific instances where customers experienced problems or were not completely satisfied with the services provided. Overall, the sentiment of the reviews is positive, with a slight inclination towards the positive side. The recurring themes in the positive reviews indicate that Jackson and Sons generally provides high-quality services and strives to meet customer expectations. However, it is important to note that the negative reviews should not be overlooked, and the company should continue to work towards improving its services and addressing any issues that may arise.
Our Reviews by City
I was very satisfied with the service I received. Everyone was quite knowledgeable and exhibited great customer service .
Bebra - Mount Olive, NC 28365
Mount OliveNC28365 35.235-78.07




Thank you so much!!
Teresa - Mount Olive, NC 28365
Mount OliveNC28365 35.1525-78.115




Fantastic Service!!
Craig - Mount Olive, NC 28365
Mount OliveNC28365 35.1925-78.085




Great
Keith - Mount Olive, NC 28365
Aidan was efficient and worked without breaks in very cold conditions
Mount OliveNC28365 35.235-78.0625



Good Service
Gene - Mount Olive, NC 28365
Mount OliveNC28365 35.1725-78.025




HVAC PM Review
Gene - Mount Olive, NC 28365
Nick provided outstanding service and provided excellent information regarding his findings when he conducted semiannual PM on our HVAC system. Want to see him again in the spring!
Mount OliveNC28365 35.165-77.98



Excellent service
Shawn - Mount Olive, NC 28365
Efficient affordable service excellent technician
Mount OliveNC28365 35.2275-78.07



Great
Keith - Mount Olive, NC 28365
Efficient. Fast. Explained the problem clearly. Friendly. MA Wright
Mount OliveNC28365 35.235-78.0625



Excellent
Tony - Mount Olive, NC 28365
Mount OliveNC28365 35.185-78.0725




Great service experience
Danny - Mount Olive, NC 28365
Mount OliveNC28365 35.2025-78.05




Excellent Service
LANE - Mount Olive, NC 28365
Mount OliveNC28365 35.2225-78.1625




Excellent Service
Rones - Mount Olive, NC 28365
Luis did a great job. Very thorough and explained everything well.
Mount OliveNC28365 35.1675-78.015



Excellent Service
Justin - Mount Olive, NC 28365
Mount OliveNC28365 35.0725-77.9225




Excellent service
Janice - Mount Olive, NC 28365
Mount OliveNC28365 35.2425-78.03




Excellent Service..
LANE - Mount Olive, NC 28365
Noah Carter was awesome. He came and got my AC back up and running .
Mount OliveNC28365 35.2225-78.1625



Great service
HAKES - Mount Olive, NC 28365
Mount OliveNC28365 35.26-78.235




Excellent
Shawn - Mount Olive, NC 28365
Great overall service!
Mount OliveNC28365 35.2275-78.07



Excellent service on our maintenance plan
HIGGINS - Mount Olive, NC 28365
The technicians are always knowledgeable and polite when they come to our home. They give us a heads up on things to watch out for based on the age of our system and what they notice upon inspection.
Mount OliveNC28365 35.2575-78.2375



Excellent service
KEEL - Mount Olive, NC 28365
Mount OliveNC28365 35.2025-78.05




Awesome Service!!
Prudencia - Mount Olive, NC 28365
Jackson and Sons continue to be professionals and very detailed
Mount OliveNC28365 35.1925-78.065



Excellent service/technician!
PETTEWAY - Mount Olive, NC 28365
The technician was such a nice young man. Very polite and knowledgeable. A pleasure having him perform the maintenance.
Mount OliveNC28365 35.2075-78.045



Great job!
MCINTOSH - Mount Olive, NC 28365
Associate was very polite and thorough.
Mount OliveNC28365 35.225-77.99



Excellent Service
MCCULLEN - Mount Olive, NC 28365
Excellent service and the technicians were very professional and Knowledgeable.
Mount OliveNC28365 35.1875-78.0675
Response from Jackson & Sons:
It was a pleasure serving you and your family. We really appreciate you taking the time to share your feedback with us and the community.




Excellent Service
Janie - Mount Olive, NC 28365
I really appreciate his mannerisms. He was professional & knowledgeable of what he was doing.
Mount OliveNC28365 35.0775-77.8925



Great service
HAKES - Mount Olive, NC 28365
Great customer service. Called for a heating issue and showed up in an hour. Technician found the capacitor was bad, explained all my options and had my heat up and running in minutes.
Mount OliveNC28365 35.26-78.235



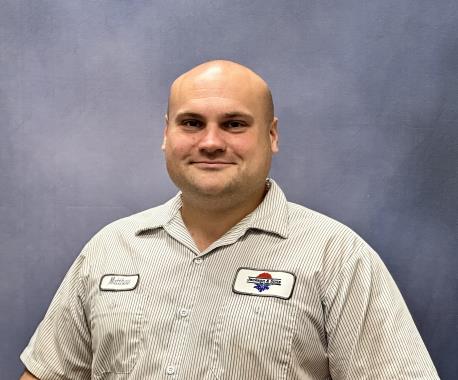
Matthew L.
Tech found red common wire between capacitor and contactor left disconnected after maintenance causing compressor not to start. Tech plugged wire back in and tested. System is back operating. Outdoor unit is 23 years old and indoor unit is 35 years old. Tech recommends system replacement. No charge for callback.
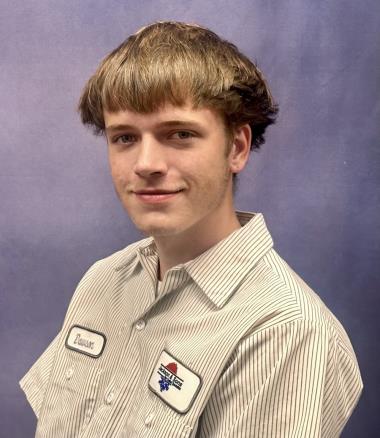
Dawson M.
Tech serviced and cleaned unit. Tech found evaporator coil to be severely rusted. Tech did a detailed leak search but could not find a consistent leak. Last tech that came out said the compressor was going from red to caution. Tech megaohmed compressor and found it in the green. Tech faced no other challenges this visit. Unit struggled to get up to Temperature with a delta t of 19 for heat. Tech informed customer about the age of the unit and how the efficiency is not the same as it was before it first got put in. Customer said she will call in for a estimate on a new system.
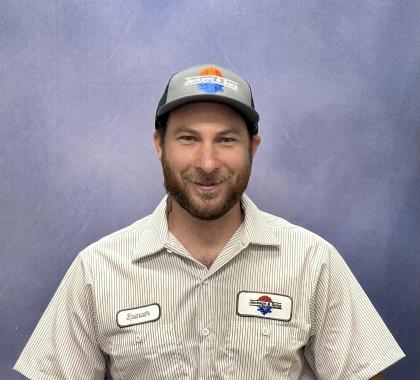
Spencer C.
Tech performed CMA full service and replaced filters. System is in a dirty environment and recommend UV light and/or plasma for better indoor air quality. System is maintaining temp at this time.
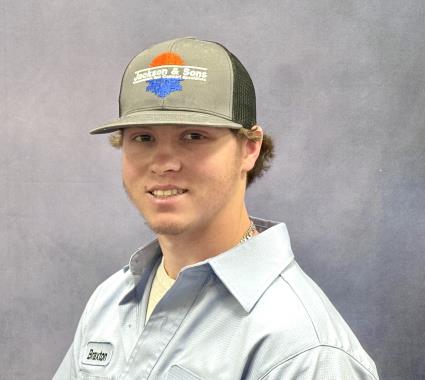
C. Braxton B.
Tech cleaned and serviced unit tech found no challenges at this time unit is up and working properly
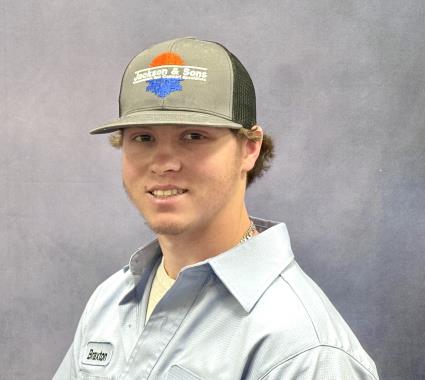
C. Braxton B.
Tech cleaned and serviced unit tech found no challenges at this time unit is up and working properly

Kyle W.
Performed CMA on (1) Trane Split Heat Pump. Changed filter. System operating properly. Added AC renew after approval.
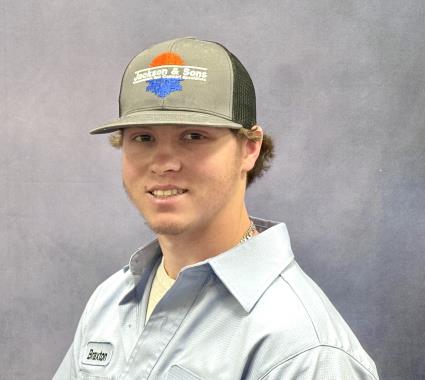
C. Braxton B.
Tech cleaned and serviced unit tech found no challenges at this time unit is up and working properly
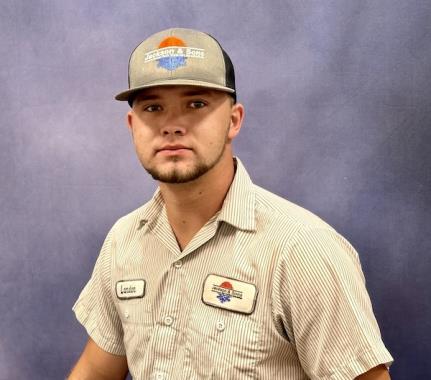
Landen H.
Apon arrival tech found upstairs air handler to be blank tech checked breaker and found breaker to be in the off position with line voltage un hooked, after last weeks storm they had some electrical issues and had electrician come out, tech spoke with electrician on the phone and he stated that he wasn’t aware they the breaker ran a thing because it was in the off position so he un wired and used the neutral block to feed another breaker tech rewired breaker and conjoined ground to another ground block, tech insured unit have have power and up and running properly at this time. Customer is having all new breakers and breaker panels installed in 2 weeks. (Was not caused by previous maintenance)
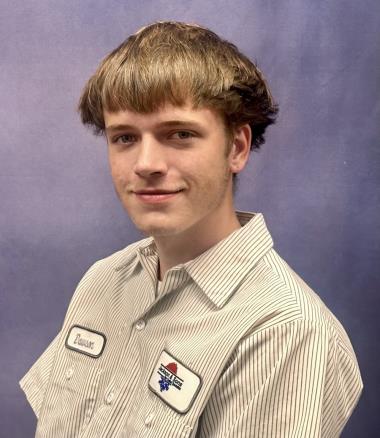
Dawson M.
Tech serviced and cleaned unit. Tech faced no challenges this visit (unit is only a couple months old). Unit is heating and cooling efficiently. Tech recommends plasma air to prevent bacteria build up in the future. Customer declined.

Audonel G.
Install Trane 3 Ton Package Unit With Plasma Air With WiFi Programmable Thermostat
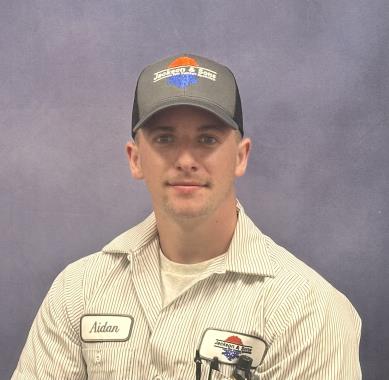
Aidan T.
— Tech leak searched the evaporator coil with two leak detectors to confirm previous diagnosis, finding no leaks or refrigerant residue. — Checked refrigerant charge according to PT chart, finding accurate refrigerant charge and no challenges heating or cooling. — Tech advised customer of rust formation on the coil and proposed replacing the coil while still under warranty before a leak develops in the future. Customer opted not to replace the coil at this time. — Confirmed proper heat strip and defrost operation. System is operating normally at this time. No charge per recent visit.
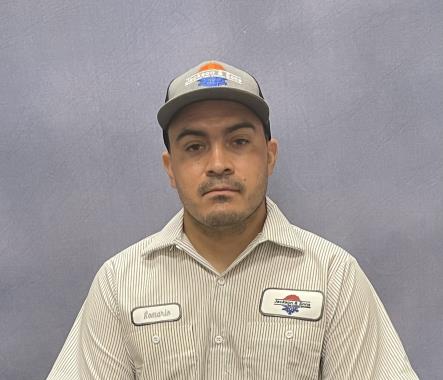
Romario T.
Downstairs package system. Tech found a failed indoor psc blower motor, extremely hot to the touch. Capacitors checked good. 2007 system R22, meg on the good level. Customer would like to consider system replacement due to age and high repair bills, Tech requested a field supervisor to provide a solution. Field supervisor is aware and will contact the homeowner. Downstairs system is down.
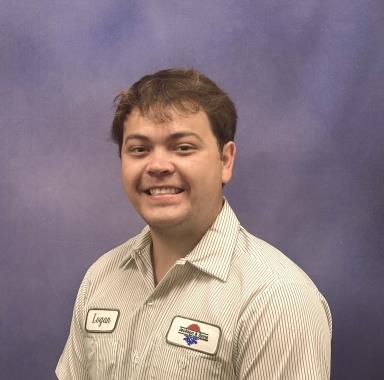
Logan P.
Tech performed service on heil package unit. Tech installed 20x20x3 media filter and cleaned return grille all ok at this time. Customer renewed maintenance plan. Delta t is within specification. Found no other challenges at todays visit.
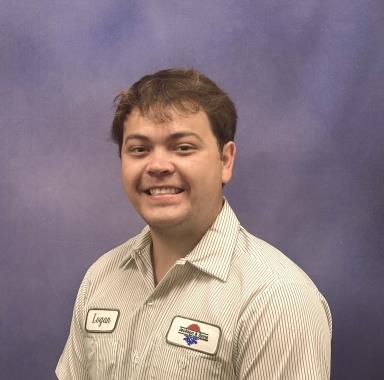
Logan P.
Tech performed service on trane package unit. Upon arrival, tech heard noise coming from unit. Found inducer draft motor to be failing. Tech informed customer about situation, as well as installation of Hard Start Kit. Customer declined repairs today for future but stated will call office to get situation resolved. Tech was unable to receive delta t due to no gas. Customer stated has not filled tank and will refill as soon as possible. Found no other challenges at today’s visit.
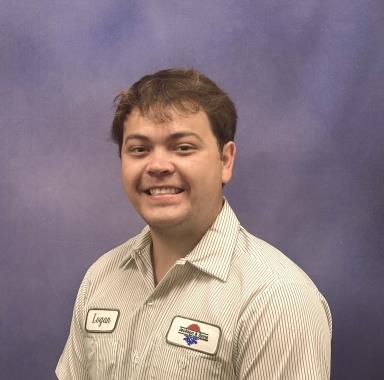
Logan P.
Tech performed service on American Standard package unit. Delta t is little lower than specification. Tech informed customer about age and efficiency of unit. Customer is aware at this time and stated knew age of unit and thinking of replacement in future. No further action was taken. Found no other challenges at today’s visit.
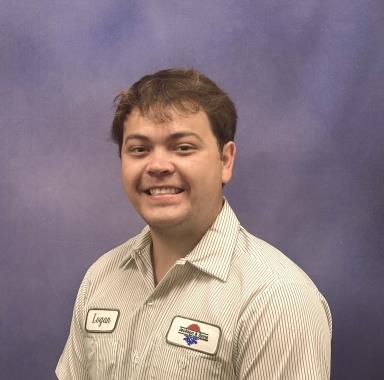
Logan P.
Tech performed service on trane package unit. Customer renewed maintenance plan. Delta t is within specification and customer is satisfied with today’s service. Found no other challenges at today’s visit.
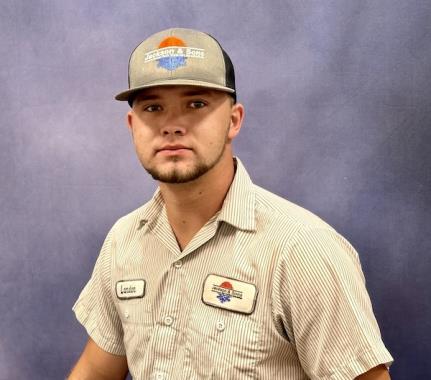
Landen H.
Tech washed and serviced both units and found no challenges with the units at this time both systems are fairly new tech did see come insulation had come off part of the upstairs duct sys tech re taped insulation to prevent condensation issues tech found no other challenges at this time. Both systems are up cooling properly after todays visit.
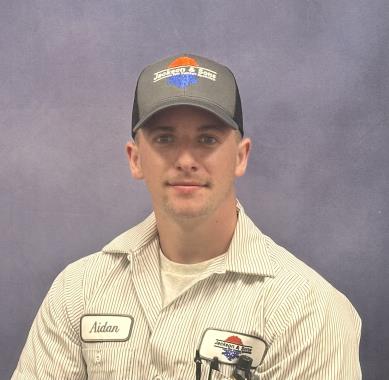
Aidan T.
— Tech replaced failed defrost control board on Oxbox split system and confirmed operation. — Serviced condenser unit per service agreement (no water access) and could not access air handler, per customer request. Provided two 20x20x1 air filters, customer recently replaced. System is operating normally at this time.
Jerry H.
Tech serviced and cleaned unit tech found no challenges at this time unit is up and working properly
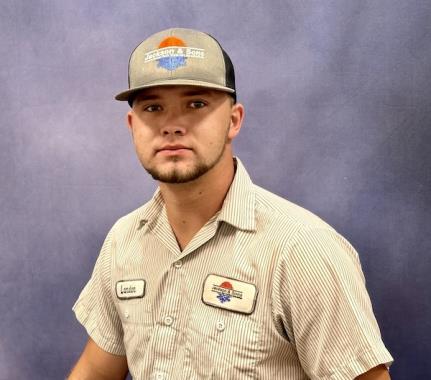
Landen H.
Tech washed and serviced unit and found no challenges at this time customer extended esa 1 sys 2 times a year. Unit is up and cooling properly after today’s maintenance.
Jerry H.
Tech cleaned and serviced unit tech did find a bad Uv bulb customer did want it replaced tech found a bad coil set up mandatory customer wants to go with replacement tech found no other issues at this time unit is up and working properly

Bryce C.
Provided estimate for evap coil replacement as well as system replacement. Customer opted for evap coil replacement under warranty
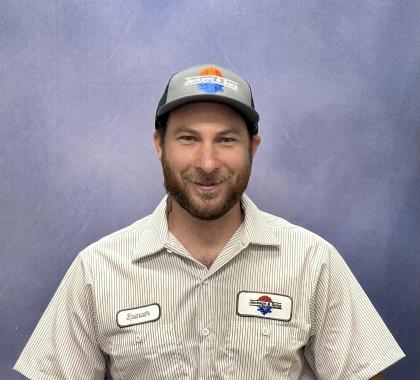
Spencer C.
Tech was in formed only 1 system is heating. Tech found the unit by the back door blower and heat strips not running. Tech found the sequencer only sending power on 1 level. Tech found when power on g, blower is not running. Tech found when relay is bypassed, blower will run. Tech found 3 open fuse links and a broken heating element. The other element was loose. Tech quoted a sequencer, relay, restring 2 heat kits, and replace 3 fuse links. System is in overall poor condition and should consider replacement. Tech found the kitchen system trying to run heat, but is an AC only system. Tech found oil stains on condenser coil and quoted a leak search.
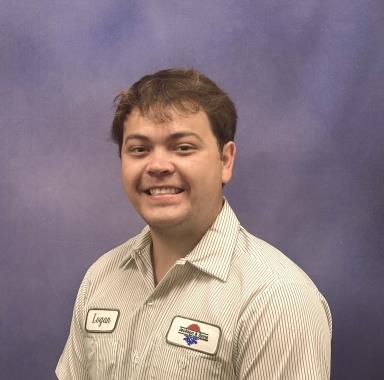
Logan P.
Tech performed service on goodman package unit. Delta t is within specification and customer is satisfied with today’s service. Found no other challenges at today’s visit.

Chris A.
Tech washed and serviced unit, compressor ohming yellow and evaporator coil is in rough shape. No leaks detected and unit is holding a delta T of 18. Customer is aware of units age and condition. Used a 14x20