Dunn NC Heating & Air Conditioning Services
Expert Local HVAC Services in Dunn, NC
Looking for a reliable heating and air conditioning company in Dunn, NC? Look no further than Jackson & Sons! Our expert team is passionate about providing top-notch service for all of your residential HVAC needs. Whether you need repairs, replacements, new installations, or maintenance, we've got you covered. We also offer indoor air quality products, ductwork repair and installation, and dryer vent cleaning to ensure that your home is as safe and comfortable as possible.
Our team is highly trained and knowledgeable and we take pride in offering same-day service whenever possible. But what truly sets us apart is our commitment to our community - we care deeply about our customers and their satisfaction. That's why we're the top-rated HVAC company in the area! Don't just take our word for it - read some of our glowing reviews from other satisfied customers near you to see why Jackson & Sons is the right choice for all of your heating and air needs. When you're ready, give us a call at (919) 636-6222 to get started!
Local Reviews
for Dunn, NC
Customers say: The reviews exhibit a positive overall sentiment, with a significant number of reviews expressing satisfaction and praise for the services provided by Jackson and Sons. The positive reviews highlight aspects such as excellent service, polite and informative technicians, quality installations, and friendly and helpful office staff. The recurring themes in the positive reviews include professionalism, punctuality, and the ability to address customer concerns effectively. However, there are also a few negative reviews, which primarily focus on issues such as delayed response times, scheduling conflicts, and dissatisfaction with the quality of work. The negative reviews mention specific instances where customers experienced problems or were not completely satisfied with the services provided. Overall, the sentiment of the reviews is positive, with a slight inclination towards the positive side. The recurring themes in the positive reviews indicate that Jackson and Sons generally provides high-quality services and strives to meet customer expectations. However, it is important to note that the negative reviews should not be overlooked, and the company should continue to work towards improving its services and addressing any issues that may arise.
Our Reviews by City
Great Affordable price for an Inspection along with great service
Robbyn - Dunn, NC 28334
I called to have an inspection for my ac/heating system because I HAD a really bad experience with another company that installed my heating/air. Spencer came out and assured me everything was ok. I will be using them after my other warranty goes out.
DunnNC28334 35.2525-78.4225



Efficient, professional, and friendly
5jinglebells - Dunn, NC 28334
DunnNC28334 35.28-78.57




Excellent
Jacob - Dunn, NC 28334
Friendly and nice
DunnNC28334 35.2275-78.525



Great
Lydia - Dunn, NC 28334
Quite, polite, Knowledgeable, committed to his job. Well pleased.
DunnNC28334 35.3125-78.625



Excellet Service
Miriam - Dunn, NC 28334
DunnNC28334 35.3375-78.555




Superb Prossionalism
Justin - Dunn, NC 28334
Outstanding work. Matthew was very professional, knowledgeable, and friendly. I would trust Matthew and recommend him.
DunnNC28334 35.335-78.6025



Excellent service
Margaritta - Dunn, NC 28334
DunnNC28334 35.22-78.57




AC Service
WINGATE - Dunn, NC 28334
I appreciate the AC service provided for my older mother. After further analysis, I felt robbed and unappreciated as a customer by your company. I contacted your company after a local company failed to show. I was disappointed with the time it took to arrive on yesterday (told it would be mid-morning), the lack of respect for my time that led to my being late for work, disappointment with the additional charge requested to search for a leak that was thought to exist ($318), not going into the attic to check the split AC system, charging $106 per lb. for R410A, when the average cost is $65 lb. and a final charge of $554 just to add refrigerate to a small AC unit. It feels like your company took advantage of a senior citizen with this extreme charge. This is very sad...I will make sure to share our experience with other potential customers, the BBB and the AG's office.
DunnNC28334 35.3275-78.6025
Response from Jackson & Sons:
Good Afternoon, Our service manager, Adam Thompson has tried to reach you by phone and was unable to leave a message. Please feel free to contact him at your convenience. If you call after 5pm, our after hours phone service will take a message and Adam will return your call. We open at 7:30 am tomorrow and close at 5pm, Adam will be in office all day except during his lunch hour from 11:30 am till 12:30 pm.




Good job has been done
TOBACCO - Dunn, NC 28334
Excellent service and I did sign up a contract to service my home
DunnNC28334 35.295-78.595



Great Service, Awesome plan
JOSE - Dunn, NC 28334
DunnNC28334 35.325-78.6225




Good service
DREXEL - Dunn, NC 28334
Jackson and sons always send good techs to my home and today was no different. Romario was courteous, knowledgeable and friendly.
DunnNC28334 35.3225-78.61



Excellent service
Ruth - Dunn, NC 28334
The technician was very professional
DunnNC28334 35.3375-78.6025



Great Service
Alexa Hernandez - Dunn, NC 28334
Seth has excellent customer service and communication skills. He explained the entire maintenance process as well as the plans available for purchase. I will continue to schedule maintenance services with Jackson and Sons.
DunnNC28334 35.3225-78.6125



Great Service
Thomas - Dunn, NC 28334
Every time I have had a problem, Jackson & Sons has been here. Brandon is very polite and know his business.
DunnNC28334 35.305-78.605



Awesome Service!! Every time I need them they come as soon as they can.
Kathy - Dunn, NC 28334
DunnNC28334 35.305-78.605




Awesome Service!! Every time I need them they come as soon as they can.
Kathy - Dunn, NC 28334
DunnNC28334 35.305-78.605




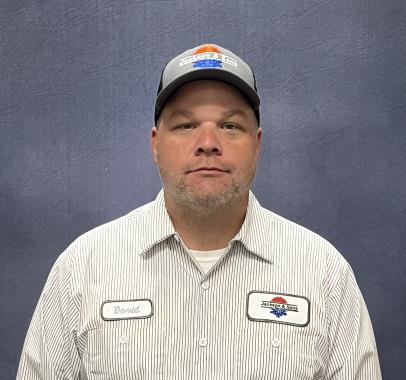
David S.
— Performed CMA Inspection on 82 Rooftop Exhaust Fans. Checked operation, greased bearings as able, inspected condition of belts & fan blades. Inspection reports provided with pictures. Smaller Rooftop Exhaust Fans are not on Service Contract, per office. — Exhaust Fan A03: Motor belts missing. Recommend installing 2-A48 belts. Provided estimate. System should be tagged out pending belt replacement. Provided estimate to install (2) A48 belts. Remote grease fitting hose ruptured prior. Recommend replacement of hose. — Exhaust Fan A04: Observed excessive noise from bearing, even after lubricating. Recommend replacement of axle bearings. System should be tagged out to prevent early failure of motor. — Exhaust Fan A07: Remote grease fitting hose ruptured prior. Recommend replacement of hose. Minor noise still present. — Exhaust Fan A09: Observed excessive noise from bearing, even after lubricating. Recommend replacement of axle bearings. System should be tagged out to p
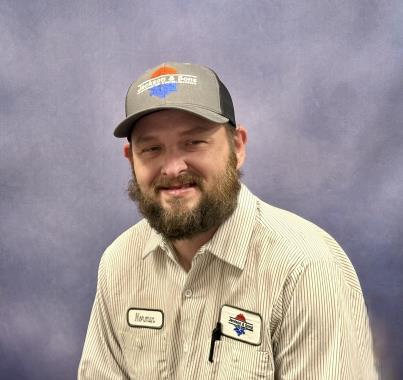
Norman A.
Fill valve not installed right doesn’t have washer are nut at bottom angle stop is not put on
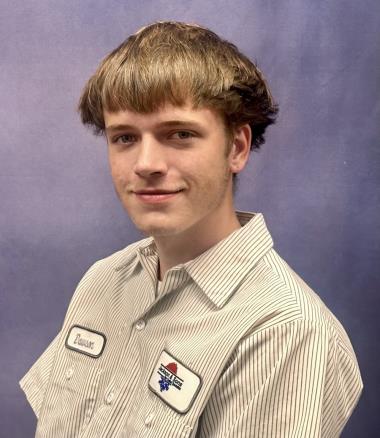
Dawson M.
Tech serviced and cleaned unit. Tech found compressor side of capacitor reading at 43.5/40 (44=bad). Tech recommends replacing soon. Tech faced no other challenges. Unit is heating and cooling efficiently.

Chris A.
Tech washed and serviced unit, found old burnt out Uv bulb in carrier package unit. Reccomended replacing, customer not interested at this time. System is up and running holding a delta T of 21. Did not have 24x24x1 filter on truck customer provided filter.

Chris A.
Tech washed and serviced unit, found no challenges with system. Dehumidifier was in need of changing filter, customer approved. Customer also approved ESA renewal. Units holding a delta T of 22.
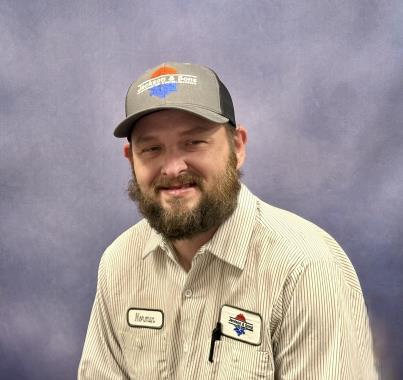
Norman A.
Fill valve not installed right doesn’t have washer are nut at bottom angle stop is not put on right
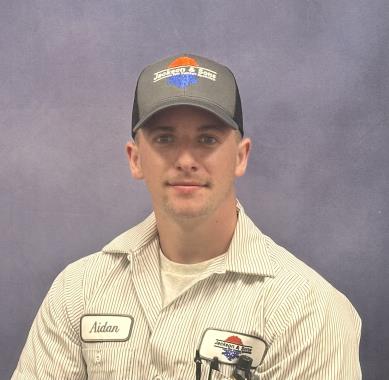
Aidan T.
— Tech found tripped compressor breaker upon arrival and inspected compressor, observing grounded windings and failed compressor. — Isolated compressor from the electrical circuit and confirmed proper condenser fan operation and heat strip operation. Customer approved warranty estimate to replace. Need to order a replacement (2 stage) compressor and expedite scheduling for installation. R-410A factory charge 11.2lbs. Auxiliary heat is operating normally at this time.

Chris A.
Tech washed and serviced unit, found no challenegs at this time. Unit is heating with a delta T of 20. Used a 20x20x1

Chris A.
Tech washed and serviced unit, tech found no challenegs at today’s visit. Customer is interested in installing surge protector 8n the future on air handler disconnect. Due to disconnect burning up before (left estimate). Unit is holding a delta T of 21. Custoemr has washable filters.
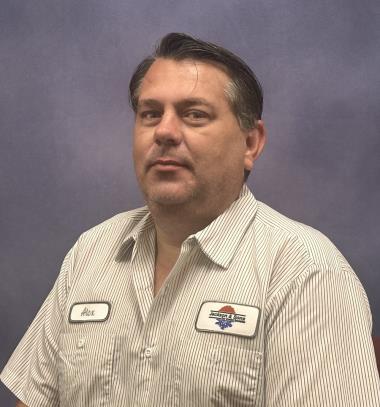
Alex R.
Water heater is not leaking. The water heater needs a new gas valve and thermal coupling to work properly. Quoted between 400-700 to get a new gas valve and thermal coupling and install them. The water heater is a 2014 model. My professional opinion would be to replace the unit due to its age and not putting money into trying to repair the unit.

Caleb S.
Provided estimate to replace heat pump
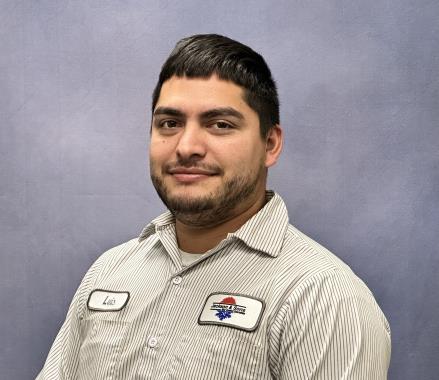
Luis R.
Technician found od fan motor bearings are failing causing loud grinding noise from od fan motor. Technician also leak searched and found a small hit on bottom of evaporator coil. Technician spoke with office on findings field supervisor is dispatched but customer is having to go back to work so field supervisor is going to call and go over her options.
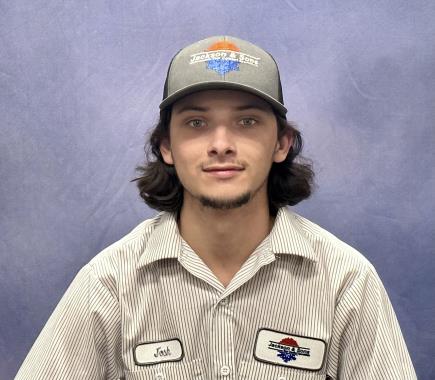
Josh W.
Tech arrived and spoke to Mr Wiles, customer stated filter change was completed in January but 6 to 10 filters were lift in roof. Te h removed old filters from roof. All is good at this time.
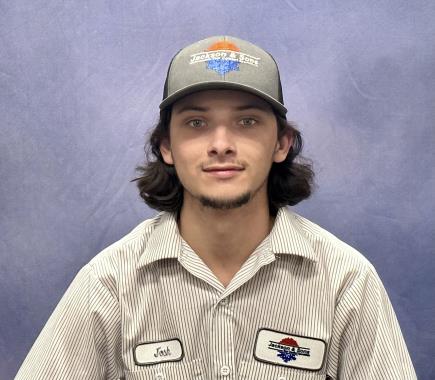
Josh W.
Tech arrived and found system running, tech found system to be struggling to keep up due to reduced airflow through system. Tech found filter and evap coil to be severely covered in dust debris and bacterial growth. Tech cleaned coil and informed tenant of how often filters need to be changed system is back on and cooling with 24 degree delta t through all supply’s. Bill out
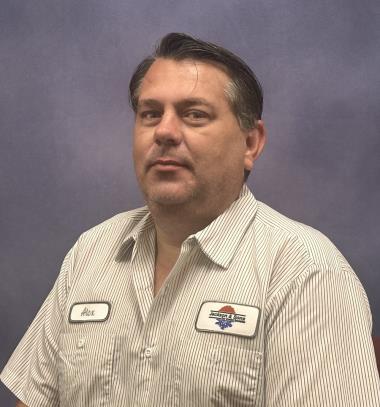
Alex R.
Cut out old faucet and installed a new customer supplied moen Faucet.
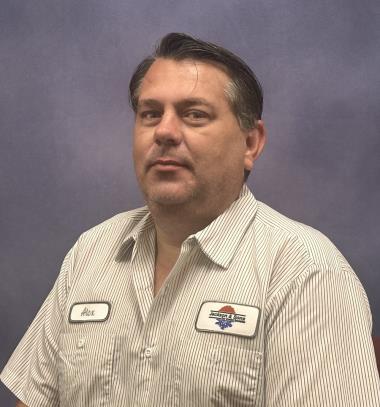
Alex R.
Found the handheld pull out sprayer for the kitchen faucet was leaking into the bottom of the kitchen cabinet. Customer is going to replace kitchen faucet himself.
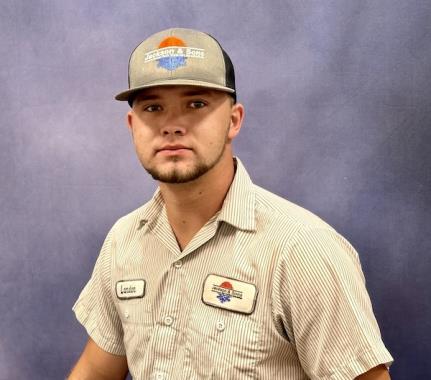
Landen H.
Apon arrival customer informed tech that unit wasn’t doing anything tech found air handler to have no power tech found disconnect to be burnt up and melted tech informed customer that we could replace disconnect and wires to unit and also recommended surge protection but could not promise that it would not happen again tech recommended having electrician come out to replace wires from breaker panel to disconnect customer paid house call and will call after electrician fixes wires for maintaince.
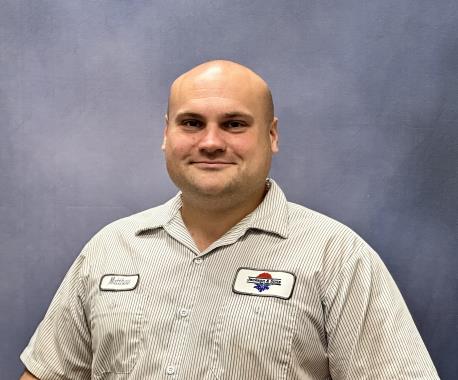
Matthew L.
Tech found system not operating due to a tripped float switch and clogged drain. Also found no filter in indoor unit. Installed 20*20 filter. Let Raquel know of findings about drain who approved drain cleaning. Tech cleared drain and tested system. System is back operating. There was a miscommunication about billing vs collecting at time of service. Our office approved billing and requested payment within 30 days.
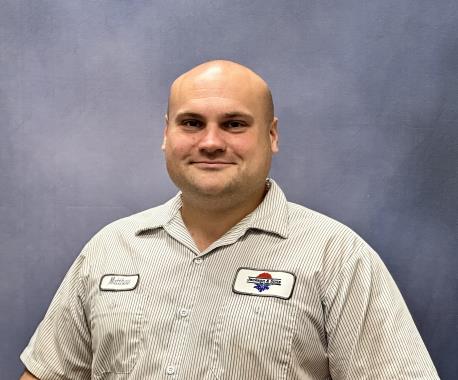
Matthew L.
Tech returned and replaced failed igniter with OEM hot surface igniter. Tech tried to check inlet gas pressure, but pressure tap is stripped out. Once burner lit, tech found manifold pressure on negative pressure burner to be -0.1 " WC. Tech adjusted it to -0.2" WC per data plate. Tech billed for repair. System is heating. Tech recommends getting all systems in CMA commercial maintenance.
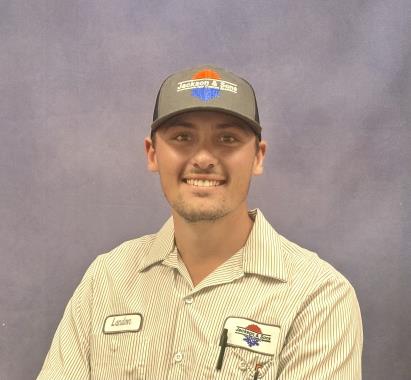
Landon C.
Field supervisor provided customer with proposal for replacement system.
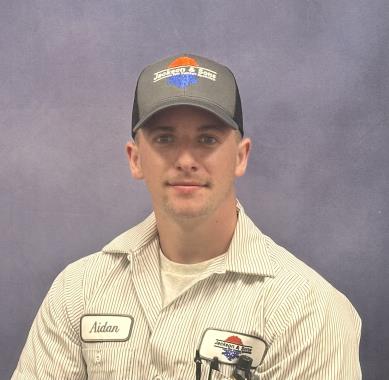
Aidan T.
(1999 Ruud Gas Pack) - Customer informed tech that the system runs intermittently, but not consistently when thermostat is calling for heat. - Found corroded burners, flame sensor, and igniter. - Found heavily damaged fire wall with holes exposing the air supply to the burner section of the system; previously repaired by another company. Inspected the heat exchanger and observed no damage. - Recommended system replacement on account of age, costly repairs, and safety concerns. Turned over to field supervisor and will provide estimate tomorrow. Turned power and gas off.
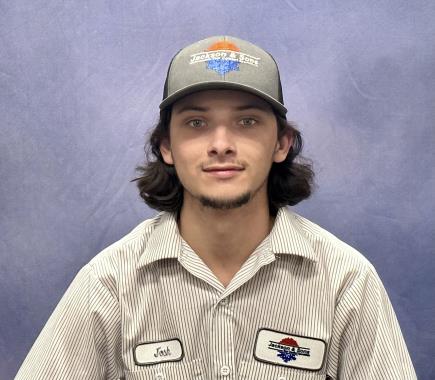
Josh W.
- Techs relocated thermostat due to inability to access existing line in the attic (mobile home). - Replaced full length of thermostat wire and installed no splices. Installed a Vision Pro thermostat and did not connect to Wi-Fi or scheduling per customer request. - Sealed old thermostat wire holes and confirmed proper operation. System is operating normally at this time.

Bryce C.
Provided quote to replace gas furnace
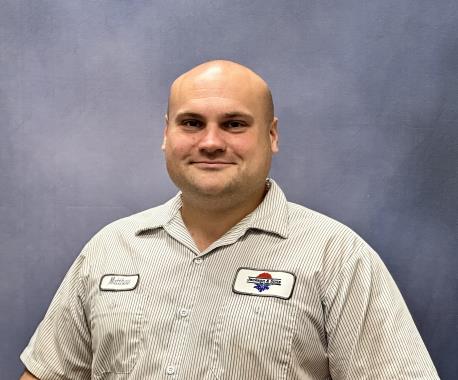
Matthew L.
Tech found large 12 year old Trane Voyager gas pack not heating. Tech confirmed failed igniter. Tech confirmed it is getting 108 volts, but not glowing. Customer reports igniter has been replaced 6 or 7 times recently. Says system will heat for a little while until igniter fails again. Tech could not remove top screw holding igniter in place. Placed WD40 on screw. System has a negative pressure gas valve that requires -.2" WC upon ignition. Tech confirmed gas valve is working properly. Installation manual says unit needs 2.5" WC natural gas supply to unit. Tech recommends ordering OEM part and verifying gas pressures with gas pack running in heat. Unable to determine why gas pack has had 6 or 7 failed igniters at this time. Brian Mcneill approved ordering OEM igniter and returning to replace and verify gas pressures. Let him know that there may be more underlying issues that will need to be repaired. Billed service call per office.
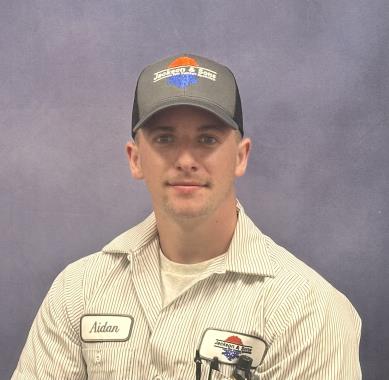
Aidan T.
- Tech found blank Focus Pro 5000 thermostat upon arrival due to failed fuse. - Examined all low voltage wires in compressor compartment, finding no shorts. - Inspected each thermostat wire individually noting no continuity or ohm resistance between any wires, disconnected from equipment and thermostat. Disconnected thermostat wires from equipment and energized each circuit individually, finding no challenges with operation. Reconnected thermostat wires to equipment and energized each thermostat wire manually, observing fuse failure when Y1 circuit is energized. - Thermostat wires are shorted and need to be replaced. Two technicians are required to replace full 30’ (approximate) length of wire. - Tech isolated G, C, R, and W circuits to operate the heat strips until the thermostat wire is replaced. Advised customer to only use emergency heat setting on thermostat. Office will contact customer regarding price for repairs. Customer is not home until 15:30; indoor access is required.